1. Equipment Composition
-
-
Uncoiler
-
Shear & End Welder
-
Accumulator
-
Forming and Sizing Mill
-
High Frequency Induction Welder
-
Inner and Outer Burr Remover
-
Water Cooling Section
-
Sizing and Straightening Unit
-
Automatic Flying Saw / Cold Saw
-
Run-out Table
-
Electrical Control Cabinet (PLC System)
-
Hydraulic System
2. Technical Parameters
-
Item |
Specification |
Tube Diameter |
21.3mm – 76mm |
Wall Thickness |
1.0mm – 4.0mm |
Pipe Shape |
Round / Square / Rectangle |
Материјал |
Carbon steel / Galvanized steel |
Line Speed |
Up to 90 m/min |
Welding Method |
High Frequency Induction |
Cutting Method |
Flying Cold Saw or Friction Saw |
Power Supply |
380V / 415V, 50Hz / 60Hz, 3-phase |
Control System |
Siemens PLC + HMI |
-
-
- 3. Equipment Advantages
-
High Stability and Reliability: High-quality components with low failure rates and simple operation, reducing manual intervention.
-
Versatile Application: Suitable for producing small to medium-diameter straight seam welded pipes, widely used in construction, machinery, oil, and other industries.
-
Cost-saving: By reducing downtime and optimizing the production process, operating costs are minimized.
-
High-quality Tubes: Advanced welding technology ensures that the tube quality meets industry standards.
-
Saudi Customer Case: 3 sets of 12.7mm-50.8mm straight seam welded pipe mills were successfully commissioned in Saudi, helping the customer enter new markets and meet the demand for small to medium-diameter steel pipes in the construction and machinery manufacturing sectors. The customer reported that the equipment was easy to operate, highly efficient, and stable, greatly improving production efficiency.
-
Mexico Customer Case: In the Mexico, a company purchased several 12.7mm-50.8mm ERW tube mills to produce tubes mainly used in the renewable energy sector. The high precision and production capacity of the equipment helped the customer tap into new markets, significantly boosting profitability.
-
China Customer Case: A large steel pipe manufacturer in China uses this equipment to produce welded pipes widely used in the petrochemical industry. The equipment runs stably, and the customer reported that it adapted well to various operating conditions, offering improved production efficiency, reduced maintenance costs, and high-quality output.
The Technical Flow of the Production Line
Steel coil → Uncoiling → Shear & End Welding → Accumulating → Forming → HF Welding → Inner burr removal → Outer burr removal → Cooling → Sizing → Straightening → Cutting → Run-out → Packaging
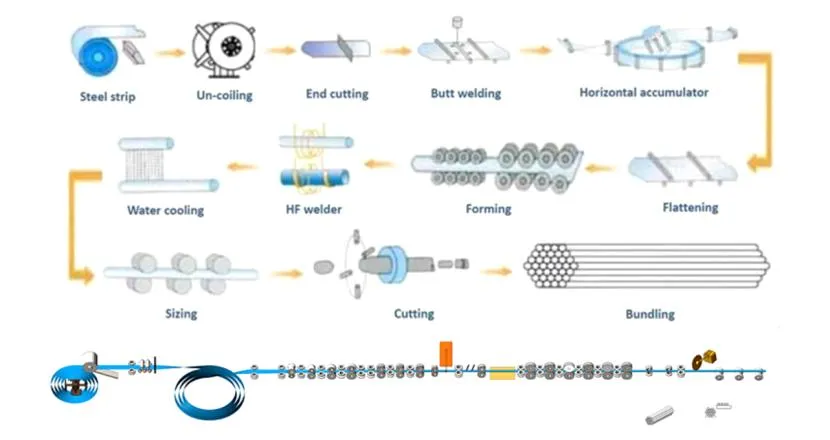
5. Customer Feedback
-
Mexico – A customer adopted a 76mm line for producing mechanical tubing used in gym equipment, achieving stable production and cost efficiency.
-
Indonesia – 21.3–60mm tube mill for construction scaffolding, with cold saw cutting to improve weld surface finish.
-
Poland – Line exported to manufacture furniture tubes with tight tolerances; praised for its automation level and speed.
6.Tube Application Scope:
-
7. Production Notes:
-
Maintain alignment during forming to avoid weld defects.
-
Ensure clean, dry steel strips for consistent welding.
-
Adjust HF welder power according to wall thickness.
-
-
8. Packaging and Transportation:
-
Machine modules are film-wrapped and fixed in steel frames.
-
Electrical and hydraulic parts are packed in moisture-proof wooden boxes.
-
Each shipment includes a user manual, wiring diagram, and spare parts list.
-
Export standard compliant with CE, ISO, and customer destination customs requirements.