Production speed is a critical metric for moinho de tubos operations, directly impacting productivity, cost efficiency, and customer satisfaction. As a wholesaler, understanding how to optimize speed across laminador de tubos and máquina formadora de tubos de aço systems—while maintaining quality—enables partners to select equipment that aligns with production goals. HEBEI AIS MACHINERY EQUIPMENT CO.,LTD specializes in engineering moinho de tubos solutions that balance speed with precision, offering configurable systems to meet diverse manufacturing needs. This guide explores the factors influencing moinho de tubos production speed, strategies for maximizing throughput in laminador de tubos and máquina formadora de tubos de aço operations, and how equipment design impacts overall efficiency, empowering wholesalers to support customers in achieving optimal production rates.
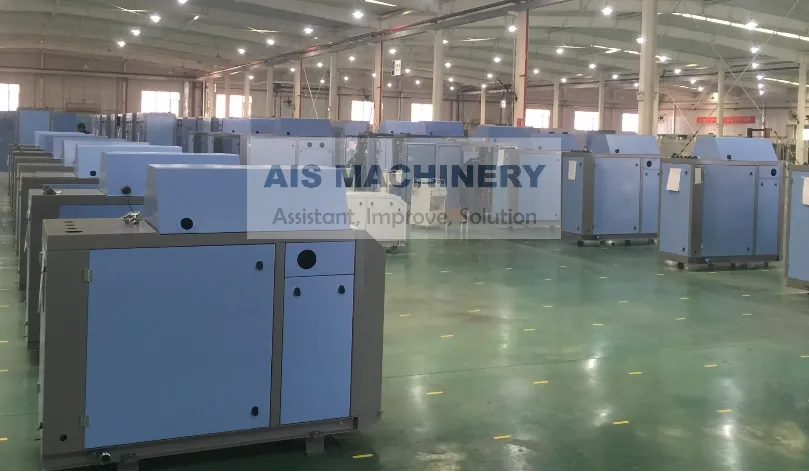
Pipe Mill Production Speed Fundamentals
Speed Metrics and Measurement
- Linear Speed Calculation: moinho de tubos production speed is typically measured in meters per minute (m/min), representing the rate at which raw material is converted into finished pipes. HEBEI AIS MACHINERY EQUIPMENT CO.,LTD.’s standard moinho de tubos models range from 20 m/min for heavy-wall pipes to 100 m/min for thin-wall, small-diameter tubes, with digital speedometers providing real-time monitoring.
- Throughput vs. Speed: While speed refers to linear rate, throughput measures total output (e.g., tons per hour), which depends on pipe size and material thickness. A moinho de tubosrunning at 60 m/min for 2" diameter pipes may produce more tons per hour than a 80 m/min system making 1" pipes. HEBEI AIS MACHINERY EQUIPMENT CO.,LTD. provides throughput calculators to help customers align moinho de tubos speed with volume targets.
- Speed Consistency: Maintaining steady speed is critical for quality—fluctuations in moinho de tubosoperations can cause uneven welds or dimensional variations. HEBEI AIS MACHINERY EQUIPMENT CO.,LTD.’s moinho de tubos systems feature servo-driven motors that regulate speed within ±1 m/min, ensuring consistent production even during long runs.
Factors Limiting Maximum Speed
- Material Thickness: Thicker materials require slower moinho de tubosspeeds to allow proper forming and welding. For example, a 10mm wall thickness may limit speed to 25 m/min, while 1mm walls can reach 90 m/min. HEBEI AIS MACHINERY EQUIPMENT CO.,LTD. designs moinho de tubos systems with variable speed controls that adjust automatically based on material input parameters.
- Pipe Diameter: Larger diameter pipes demand slower speeds in moinho de tubosoperations to ensure uniform roll forming. A 200mm diameter pipe may run at 30 m/min, while a 50mm pipe can achieve 70 m/min. HEBEI AIS MACHINERY EQUIPMENT CO.,LTD.’s moinho de tubos configurations include modular roll sets optimized for specific diameter ranges, balancing speed and precision.
- Welding Requirements: High-integrity welds in moinho de tubosproduction—critical for pressure applications—often require slower speeds to ensure proper fusion. HEBEI AIS MACHINERY EQUIPMENT CO.,LTD. notes that their moinho de tubos systems reduce speed by 15–20% when processing materials for API 5L or ASTM A106 standards, prioritizing weld quality over maximum throughput.
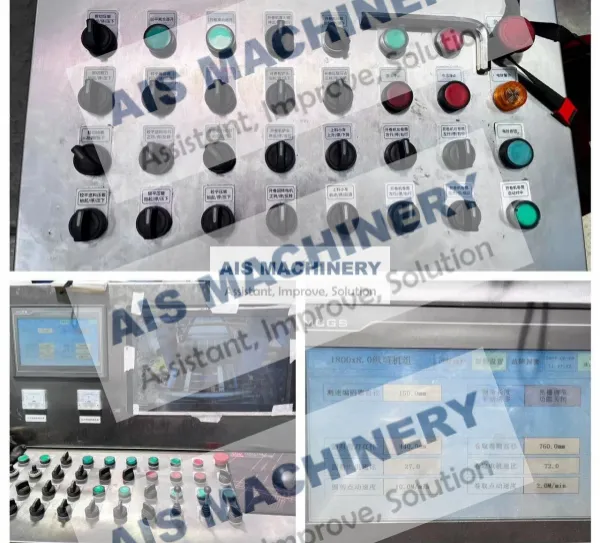
Roll Forming Tube Mill Speed Optimization
Roll Design and Speed Compatibility
- Roll Profile Engineering: laminador de tubosspeed is heavily influenced by roll profiles—optimized designs reduce friction and material stress, allowing higher speeds. HEBEI AIS MACHINERY EQUIPMENT CO.,LTD.’s laminador de tubos systems use computer-aided design (CAD) to create gradual, multi-stage forming profiles that minimize resistance, enabling speeds up to 30% higher than conventional roll sets.
- Roll Material Selection: Hardened tool steel rolls in laminador de tubosoperations resist wear at high speeds, maintaining dimensional accuracy longer. HEBEI AIS MACHINERY EQUIPMENT CO.,LTD. uses 52 HRC (Rockwell hardness) rolls for their laminador de tubos systems, suitable for continuous runs at 80+ m/min without significant degradation.
- Roll Alignment: Precise alignment of laminador de tubosrolls prevents material slippage and uneven stress, which can slow production. HEBEI AIS MACHINERY EQUIPMENT CO.,LTD. calibrates rolls to within 0.02mm of parallelism, ensuring smooth material flow even at maximum speed.
Drive System and Speed Control
- High-Torque Motors: laminador de tubossystems require powerful motors to maintain speed when processing high-strength materials. HEBEI AIS MACHINERY EQUIPMENT CO.,LTD.’s laminador de tubos models feature variable frequency drives (VFD) with 150–300 kW motors, delivering consistent torque across speed ranges to avoid slowdowns during thick material processing.
- Speed Synchronization: In multi-stand laminador de tubossetups, synchronized speed across stations prevents material stretching or buckling. HEBEI AIS MACHINERY EQUIPMENT CO.,LTD. uses servo-driven drives with ±0.1% speed matching, ensuring each forming stage operates in harmony to maintain throughput.
- Acceleration/Deceleration Controls: Smooth start-stop cycles in laminador de tubosoperations reduce downtime between runs. HEBEI AIS MACHINERY EQUIPMENT CO.,LTD.’s systems include programmable acceleration ramps, reaching target speed in 3–5 seconds without causing material distortion.
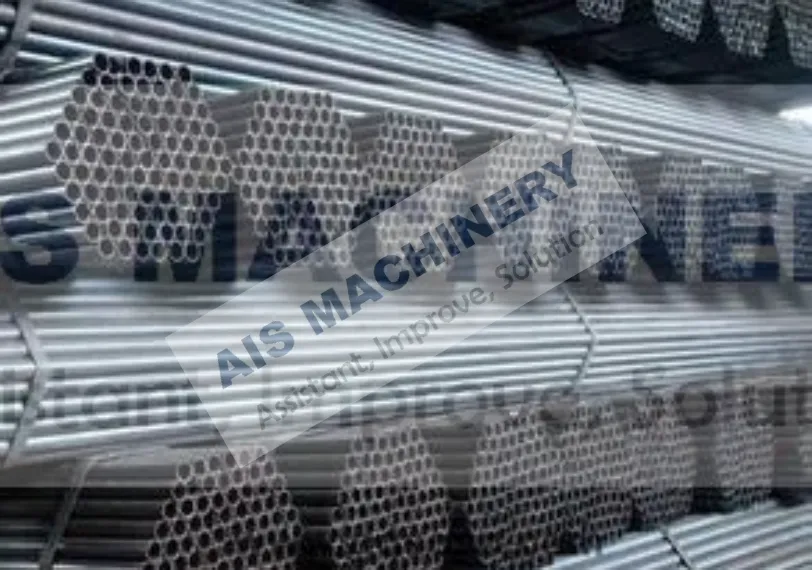
Steel Tube Forming Machine Speed and Precision Balance
Forming Stage Speed Optimization
- Progressive Speed Stages: máquina formadora de tubos de açooperations use progressive speed increases across forming stages—initial stages run slower to shape material, while final stages accelerate to boost throughput. HEBEI AIS MACHINERY EQUIPMENT CO.,LTD.’s máquina formadora de tubos de aço systems feature 6–12 forming stands with speed increments of 5–10 m/min per stage, ensuring proper shaping before high-speed finishing.
- Lubrication for Speed: Effective lubrication reduces friction in máquina formadora de tubos de açodies, allowing higher speeds without excessive wear. HEBEI AIS MACHINERY EQUIPMENT CO.,LTD. integrates automatic lubrication systems that apply precise amounts of oil or dry lubricant, enabling their máquina formadora de tubos de aço models to run at 70+ m/min for extended periods.
- Die Material Impact: Harder die materials in máquina formadora de tubos de açosetups, such as tungsten carbide, withstand high-speed friction better than tool steel. HEBEI AIS MACHINERY EQUIPMENT CO.,LTD. offers carbide dies for their máquina formadora de tubos de aço systems, supporting speeds 20–30% higher than standard dies for abrasive materials like high-carbon steel.
Welding Speed in Steel Tube Forming
- High-Frequency Welding Speed: máquina formadora de tubos de açowelding speeds depend on material thickness and pipe diameter, with high-frequency current enabling faster fusion than traditional methods. HEBEI AIS MACHINERY EQUIPMENT CO.,LTD.’s máquina formadora de tubos de aço systems use 400–600 kHz frequencies, supporting welding speeds up to 90 m/min for thin-wall tubes while maintaining weld integrity.
- Cooling System for Speed: Rapid cooling after welding allows máquina formadora de tubos de açooperations to maintain high speeds without post-weld distortion. HEBEI AIS MACHINERY EQUIPMENT CO.,LTD. incorporates water-cooled weld zones that reduce pipe temperature from 1000°C to 300°C in seconds, enabling continuous high-speed production.
- Weld Monitoring at Speed: Ensuring weld quality at high speeds requires real-time inspection. HEBEI AIS MACHINERY EQUIPMENT CO.,LTD.’s máquina formadora de tubos de açosystems include ultrasonic weld testers synchronized with production speed, detecting defects without slowing throughput.
Table: Typical Production Speeds Across Equipment Types
Equipment Type
|
Pipe Diameter Range
|
Material Thickness
|
Production Speed (m/min)
|
HEBEI AIS MACHINERY EQUIPMENT CO.,LTD. Model
|
moinho de tubos (standard)
|
10–100mm
|
0.5–3mm
|
40–100
|
AM-PM-100
|
laminador de tubos
|
50–200mm
|
2–8mm
|
20–60
|
AM-RFT-200
|
máquina formadora de tubos de aço
|
20–150mm
|
1–5mm
|
30–80
|
AM-STF-150
|
Pipe Mill FAQS
What is the maximum production speed of a standard pipe mill?
The maximum production speed of a standard moinho de tubos varies by pipe size and material, ranging from 20 m/min for heavy-wall (8–12mm) large-diameter pipes to 100 m/min for thin-wall (0.5–2mm) small-diameter tubes. HEBEI AIS MACHINERY EQUIPMENT CO.,LTD.’s versatile moinho de tubos models, such as the AM-PM-100, offer adjustable speed controls to match specific production needs, ensuring optimal performance across different pipe dimensions and materials.
How does material thickness affect roll forming tube mill speed?
Material thickness significantly impacts laminador de tubos speed—thicker materials require slower speeds to ensure proper shaping without cracking or distortion. For example, a laminador de tubos processing 8mm thick steel may run at 20–30 m/min, while 2mm thick material can reach 50–60 m/min. HEBEI AIS MACHINERY EQUIPMENT CO.,LTD. designs their laminador de tubos systems with variable speed settings that automatically adjust based on input material thickness, balancing formability and throughput.
Can a steel tube forming machine maintain high speed while producing thick-wall pipes?
A máquina formadora de tubos de aço can maintain moderate to high speeds for thick-wall pipes, though not as fast as for thin-wall tubes. For 5–8mm thick walls, typical speeds range from 30–40 m/min, compared to 60–80 m/min for 1–2mm walls. HEBEI AIS MACHINERY EQUIPMENT CO.,LTD.’s máquina formadora de tubos de aço models feature reinforced forming stands and high-torque drives to handle thick materials at these speeds, ensuring both productivity and pipe quality.
What role does roll alignment play in pipe mill production speed?
Proper roll alignment is critical for maintaining moinho de tubos production speed, as misaligned rolls cause material slippage, uneven stress, and increased friction—all of which force operators to reduce speed. HEBEI AIS MACHINERY EQUIPMENT CO.,LTD. calibrates moinho de tubos rolls to precise tolerances (±0.02mm parallelism), minimizing resistance and enabling consistent high-speed operation without sacrificing pipe dimensional accuracy.
How do roll forming tube mill and steel tube forming machine speeds compare for the same pipe size?
For the same pipe size, laminador de tubos speeds are generally lower than máquina formadora de tubos de aço speeds when processing thin to medium wall materials, as roll forming involves more gradual shaping stages. For example, a 50mm diameter pipe with 2mm walls may run at 40–50 m/min in a laminador de tubos versus 60–70 m/min in a máquina formadora de tubos de aço. HEBEI AIS MACHINERY EQUIPMENT CO.,LTD. notes that laminador de tubos systems excel in heavy-wall applications where their slower, more controlled forming produces superior results, while máquina formadora de tubos de aço systems prioritize speed for lighter-gauge pipes.
Optimizing moinho de tubos production speed requires a nuanced understanding of how equipment design, material properties, and process parameters interact. Whether through laminador de tubos systems tailored for controlled, heavy-wall production or high-speed máquina formadora de tubos de aço setups for thin-wall applications, balancing speed with quality is key. HEBEI AIS MACHINERY EQUIPMENT CO.,LTD.’s engineered solutions—from configurable moinho de tubos controls to durable tooling—empower manufacturers to achieve their throughput goals while maintaining strict quality standards. As a wholesaler, emphasizing these speed-optimization features helps customers select equipment that aligns with their production volumes, material types, and end-use requirements, ultimately driving their operational success and reinforcing your role as a trusted advisor in the industry.