Selecting the right equipment for manufacturing carbon steel tubes plays a critical role in ensuring quality, performance, and cost-effectiveness in production processes. A carbon steel tube mill, designed specifically for processing carbon steel materials, stands as a cornerstone of this manufacturing journey, offering a nexus of precision, durability, and innovation in tube production.
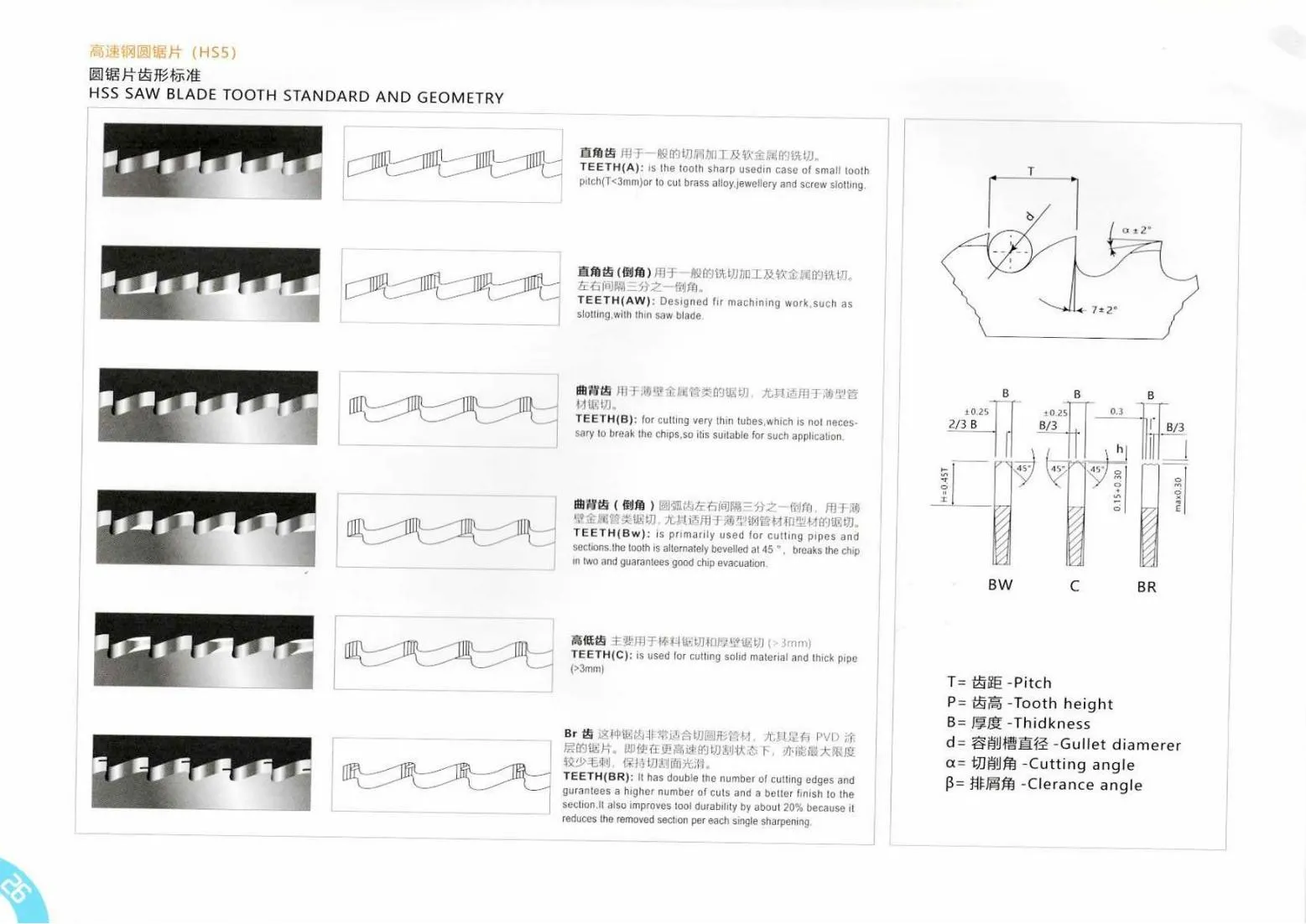
Carbon steel tube mills are engineered to handle a wide range of carbon steel grades, which are an alloy of iron and carbon along with other elements like manganese, silicon, and copper. This composition grants carbon steel notable strength and fatigue resistance, making it indispensable in construction, automotive, and infrastructure industries. A tube mill's primary function is to convert raw steel coils into high-strength tubes through meticulous forming, welding, and finishing stages, each requiring specialized equipment and expertise.
One of the fundamental advantages of a carbon steel tube mill is its capability to produce tubes of varied diameters and wall thicknesses. This versatility is achieved through adjustable forming and welding systems. State-of-the-art tube mills integrate high-frequency welding technology, which enhances the structural integrity of the tubes by ensuring uniform, high-strength welds that are essential for applications requiring high pressure and load-bearing capacities. The precision in welding is monitored via sensors and control systems that maintain consistent heat input and alignment, thus ensuring a seamless finish and reducing material wastage.
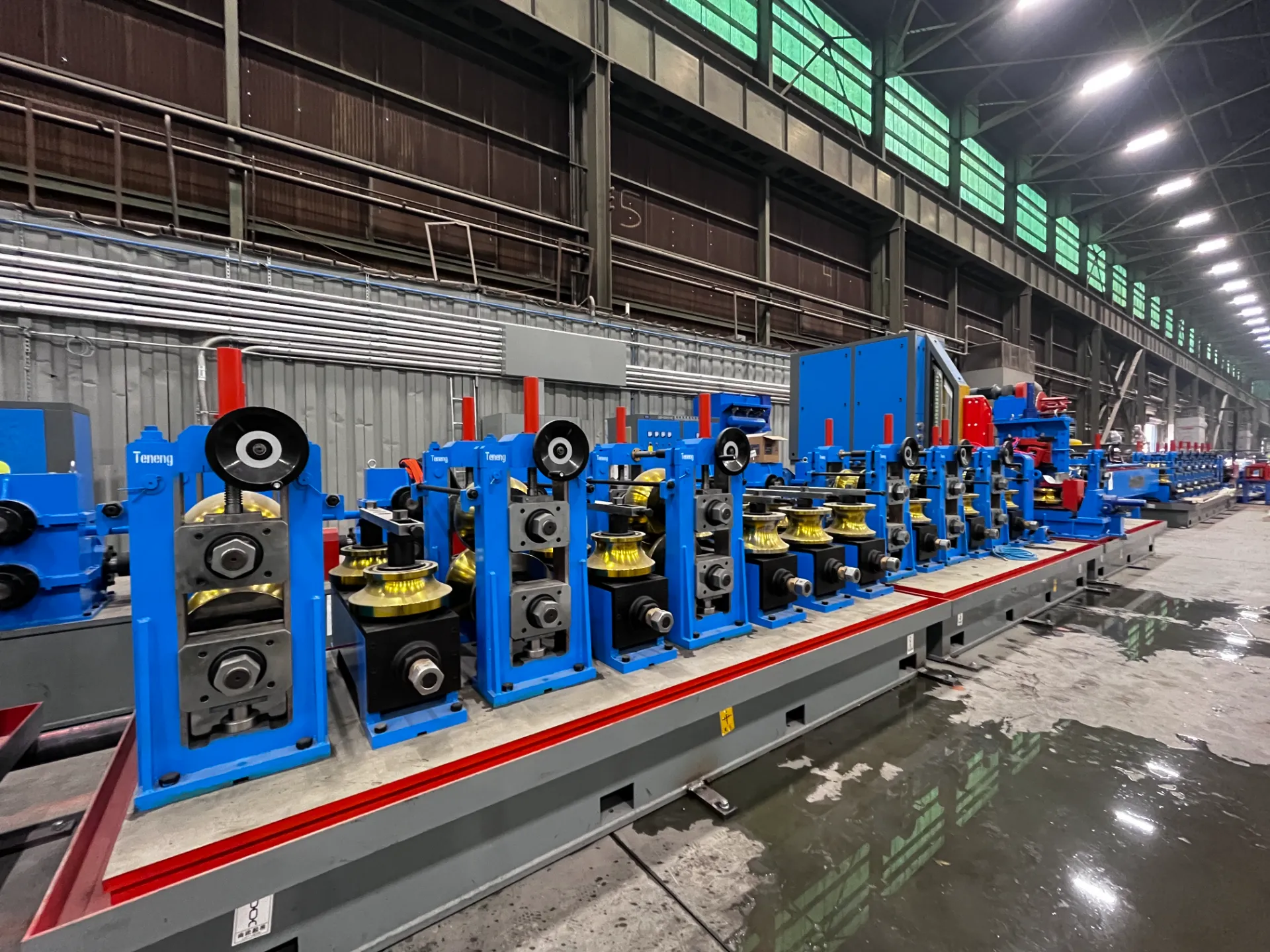
Innovation in a carbon steel tube mill is demonstrated through its adaptability to emerging technologies such as automation and digital monitoring systems. Automation has revolutionized production by reducing human error, increasing efficiency, and ensuring steady output rates. Advanced software solutions allow operators to oversee the entire production process through digital dashboards that display real-time data, enabling prompt interventions and quality adjustments to maintain industry standards.
Resource efficiency and sustainability are also pivotal aspects in the design of modern carbon steel tube mills. As environmental concerns intensify, manufacturers are increasingly incorporating energy-efficient technologies and sustainable practices to reduce carbon footprints. Advanced exhaust systems and waste recycling mechanisms are now standard in tube mill designs, ensuring compliance with environmental regulations and fostering corporate responsibility.
carbon steel tube mill
The authoritative nature of a carbon steel tube mill is further solidified by the precision and quality control measures embedded into its operations. Industry certifications and rigorous testing protocols, including dimensional inspections, mechanical testing, and non-destructive evaluations, verify that products meet or exceed specified requirements. These quality assurances not only bolster a manufacturer's reputation but also instill confidence in consumers, who rely on these products for critical infrastructure applications.
Moreover, the expertise required to operate and maintain a carbon steel tube mill cannot be overstated. Skilled technicians, trained in the nuances of metallurgy, equipment operation, and quality management, are pivotal to harnessing the mill’s full potential. Continuous training programs and workshops are essential to keep these professionals abreast of technological advances and evolving industry standards.
Historically, the development and enhancement of carbon steel tube mills reflect collaborative efforts among metallurgists, engineers, and industry leaders, culminating in a nexus of tradition and innovation.
This convergence has not only improved production efficiencies but also expanded the functional applications of carbon steel tubes, solidifying their role in modern civilization.
Thus, in exploring the dynamic world of carbon steel tube mills, it is evident that they are more than mere manufacturing apparatuses. They represent the epitome of industrial evolution—embodying expertise, innovation, and sustainability—thereby ensuring that manufacturers remain competitive and responsive to the ever-growing demands of precision and quality in today’s global market.