1. Equipment Advantages
-
High Production Efficiency: This equipment adopts an advanced automation control system to ensure fast and efficient production while maintaining continuity.
-
Precise Tube Size Control: Through high-precision sizing and straightening systems, it ensures stable product dimensions, reducing tolerance and improving consistency in finished products.
-
Material Adaptability: The equipment can process a variety of metal materials, including carbon steel, stainless steel, and alloy steel, making it suitable for a wide range of industry demands.
-
Energy-efficient and Environmentally Friendly: The equipment design meets modern environmental standards, reducing energy consumption, lowering production costs, and complying with environmental regulations.
2. Technical Parameters
-
Tube Specifications: |
Diameter range from 12.7mm to 50.8mm, wall thickness range from 0.5mm to 2.0mm.
|
Production Speed: |
Maximum production speed can reach up to 120 meters per minute.
|
Welding Technology: |
Uses high-frequency induction welding (HFW) to ensure strong and high-quality welds.
|
Sizing Range: |
Tube sizing range from 12.7mm to 50.8mm, with an accuracy of ±0.1mm.
|
Welding Current: |
Frequency range from 200KHz to 450KHz, adjustable according to tube thickness and material.
|
Electrical Control System: |
PLC control for real-time monitoring of production status, supporting remote diagnostics and adjustments.
|
Cooling System: |
Efficient water cooling system to ensure temperature control in the welding area and other equipment components.
|
Equipment Dimensions: |
Based on different models and configurations, the equipment typically occupies an area of 3000mm (length) x 1500mm (width) x 2200mm (height).
|
-
- 3. Equipment Advantages
-
High Stability and Reliability: High-quality components with low failure rates and simple operation, reducing manual intervention.
-
Versatile Application: Suitable for producing small to medium-diameter straight seam welded pipes, widely used in construction, machinery, oil, and other industries.
-
Cost-saving: By reducing downtime and optimizing the production process, operating costs are minimized.
-
High-quality Tubes: Advanced welding technology ensures that the tube quality meets industry standards.
-
Saudi Customer Case: 3 sets of 12.7mm-50.8mm straight seam welded pipe mills were successfully commissioned in Saudi, helping the customer enter new markets and meet the demand for small to medium-diameter steel pipes in the construction and machinery manufacturing sectors. The customer reported that the equipment was easy to operate, highly efficient, and stable, greatly improving production efficiency.
-
Mexico Customer Case: In the Mexico, a company purchased several 12.7mm-50.8mm ERW tube mills to produce tubes mainly used in the renewable energy sector. The high precision and production capacity of the equipment helped the customer tap into new markets, significantly boosting profitability.
-
China Customer Case: A large steel pipe manufacturer in China uses this equipment to produce welded pipes widely used in the petrochemical industry. The equipment runs stably, and the customer reported that it adapted well to various operating conditions, offering improved production efficiency, reduced maintenance costs, and high-quality output.
The Technical Flow of the Production Line
{Steel Tape}→→ Double-head un-coiler →→Strip-head Cutter and welder→→Spiral accumulator→→Forming section(Flattening unit +Main driving unit +Forming unit +Guide unit +squeeze roller)+ De-burr frame →→Cooling unit →→ Sizing unit and straightener →→Cutoff saw →→ Run-out table
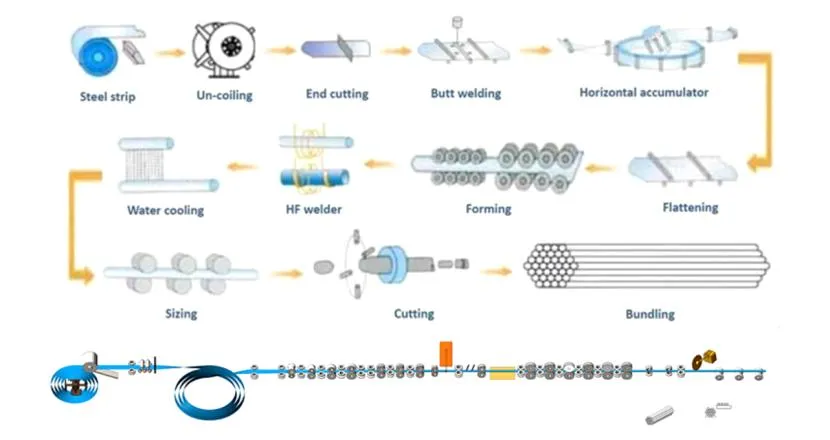
5. Customer Feedback
-
Equipment Stability: "We have been using this ERW tube mill for two years, and the production process has been stable with excellent weld quality and almost no breakdowns." — Egypt Customer
-
Ease of Operation: "The user interface is simple and intuitive, and our employees were able to operate it proficiently with minimal training." — U.S. Customer
-
Production Efficiency: "Compared to other equipment, this machine is significantly faster, with high precision, meeting our strict production standards." — China Customer
-
6. Purchasing Recommendations
-
Production Requirement Analysis: Before purchasing, evaluate your production needs, such as tube types, specifications, and quantities. Selecting the right model can significantly improve production efficiency and reduce costs.
-
Equipment Quality and Reliability: Choose manufacturers with good after-sales service to ensure the quality and reliability of the equipment, avoiding production stoppages caused by equipment failure.
-
Technical Support and Service: Technical support is a key factor when purchasing. Choose suppliers who offer comprehensive technical assistance and regular maintenance services, as this will extend the equipment's lifespan and improve overall production line efficiency.
-
Equipment Upgrades and Maintenance: Opt for models that allow for flexible upgrades to ensure the equipment can adapt to changing market demands. Additionally, regular maintenance and care are essential for maintaining stable and continuous production.
-
7. Daily Maintenance Guidelines
-
Regular Inspection of Electrical and Mechanical Components: Perform regular checks of the electrical system and mechanical components, and replace worn parts in time to ensure smooth production.
-
Cleaning and Lubrication: Clean the cooling system, lubrication system, and transmission parts, maintaining good condition to minimize wear.
-
Adjust Welding Parameters: Adjust welding current and speed according to different materials, tube diameters, and wall thicknesses to ensure the quality of the weld joints.
-
Inspect Sizing and Straightening Systems: Ensure the accuracy of the sizing and straightening systems to maintain stable tube dimensions.
-
Conclusion
The 12.7mm-50.8mm ERW tube mill equipment offers high production efficiency, precision, stability, and versatility, making it widely adopted across various industries globally. By selecting the right equipment and maintaining proper maintenance practices, customers can enhance production efficiency and meet diverse industry demands. Based on customer feedback, the equipment has shown excellent long-term performance, greatly improving production capacity and product quality.