The 10-inch ERW tube mill is designed for continuous and automated production of medium to large-diameter welded steel pipes. It transforms steel strips into round pipes through forming, high-frequency welding, sizing, and cutting processes. The equipment is highly efficient, reliable, and suitable for high-strength, high-precision steel pipe manufacturing.
Applicable pipe types include: structural pipes, fluid pipes, pressure pipes, pile pipes, and general-purpose steel tubes.
List of Equipment Supply
No.
|
Equipment Name
|
Description
|
1
|
Hydraulic Uncoiler Car
|
Transfers steel coils to the decoiler
|
2
|
Double-cone Hydraulic Decoiler
|
Automatically uncoils and holds coils (up to 15 tons)
|
3
|
Shear & Butt Welder
|
Joins the ends of two coils for continuous feeding
|
4
|
Accumulator (Horizontal)
|
Maintains tension and buffering during continuous operation
|
5
|
Forming Mill (Rough/Mid/Finishing)
|
Gradually bends the strip into round shape
|
6
|
High-Frequency Welding Unit
|
Solid-state or IGBT system with auto load matching
|
7
|
Inner/Outer Burr Removers
|
Trims internal and external weld seams for smooth pipe surface
|
8
|
Cooling Section
|
Adjustable water spray zones for weld and pipe body cooling
|
9
|
Sizing Mill
|
Ensures precise outer diameter and roundness of pipes
|
10
|
Flying Saw (Hot/Milling)
|
Servo-controlled cutting to length with anti-vibration mechanism
|
11
|
Output Conveyor & Stacker
|
Aligns, stacks, and prepares pipes for packaging
|
12
|
Electrical Control System
|
Centralized PLC+HMI interface, with real-time monitoring
|
13
|
Hydraulic & Lubrication Unit
|
Powers the system with automated oil pressure and temperature control
|
2. BASIC DESIGN DATA
Ұсынылған желіні жобалау келесі спецификацияға негізделген:
Equipment Advantages
-
Stable Construction: Heavy-duty welded frame ensures long-term durability
-
Intelligent Control: Full PLC control with alarms, diagnostics, and remote support
-
Quick Changeover: Supports multiple profiles (round, square, rectangular)
-
Excellent Weld Quality: Precision-matched HF system ensures solid welds
-
Energy Efficient: Inverter-controlled drives reduce power consumption by over 20%
-
Modular Design: Optional upgrades for stackers, cutting units, inspection systems
Welding Principle
Using high-frequency induction heating, the strip edges are rapidly heated to a plastic state, then squeezed together by pressure rollers to form a continuous weld.
-
Advantages: Smooth weld seam, small heat-affected zone, no filler material needed
-
Key Parameters: HF power adjustment, coil alignment, squeeze pressure
-
Burr Removal: Optional internal and external scarfing improves final product finish
Operating Procedure
-
Ensure all systems (electric, hydraulic, water) are operational
-
Load coil → Shear & weld → Accumulate strip → Forming & welding → Cooling → Sizing → Cutting
-
Check roll wear, blade sharpness, and induction coil daily
-
Monitor welding temperature, strip tension, and sizing output via HMI
-
Shutdown sequence: stop line → cut power → close water/air systems in order
The Flow of the Production Line
{Steel Tape}→Coil car→ Uncoiler →Peeler and hold down roll→Flattener→ Strip-head Cutter and welder→Spiral accumulator→Forming section(Flattening unit +Main driving unit +Forming unit +Guide unit +squeeze roller)+ De-burr frame →→Cooling unit →→ Sizing unit and straightener →→Cutoff saw →→ Run-out table →→Straingtener machine →→Chamfer machine →→Hydro tester machine →→automatic package machine
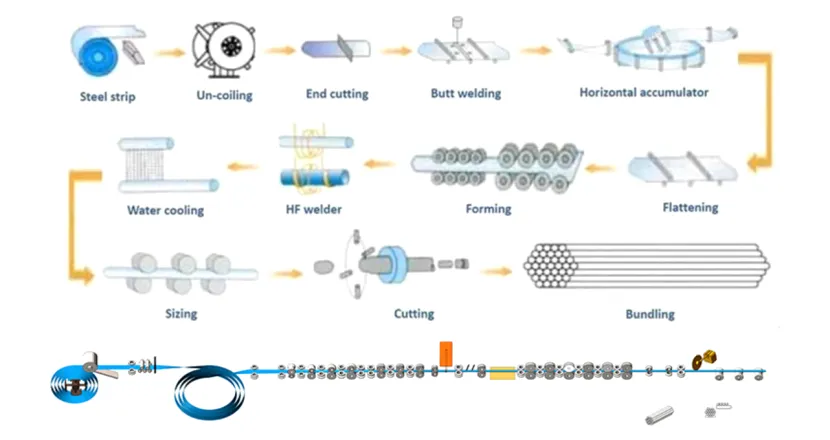
Selection Advice for Customers
-
-
Define main product specs (e.g., Φ168, Φ219) when configuring forming stations
-
Wall thickness range determines required HF power and saw type
-
Export customers should specify voltage, control language, and certification needs (e.g., CE)
-
Optional upgrades: online seam inspection, laser OD measurement, automatic stacking systems
-