Cold roll forming is an advanced metalworking process that offers a multitude of benefits for manufacturing precision components. This technology has surged in popularity across various industries due to its efficiency, versatility, and ability to produce high-strength profiles. Having spent years researching and applying cold roll forming techniques, I've witnessed its transformative influence on modern production methodologies.
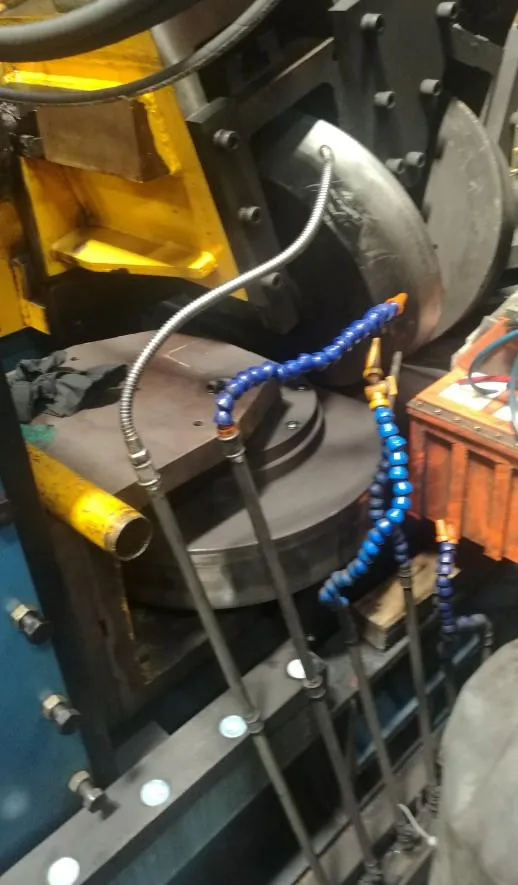
Cold roll forming involves the continuous bending of a long strip of sheet metal, commonly steel, into a desired cross-section. This process is performed at room temperature, distinguishing it from hot roll forming, which requires heating the metal. The cold roll forming technique provides superior dimensional accuracy and an impressive surface finish without the need for subsequent machining.
One of the distinguishing features of cold roll forming is its capability to produce complex cross-sections that are uniform over long lengths. This precision is due to the use of a series of carefully designed roller dies through which the metal passes. As the material progresses through these dies, it gradually takes on the shape of the final product. By carefully calibrating the dies, manufacturers can produce intricate profiles with tight tolerances, meeting even the most exacting specifications.
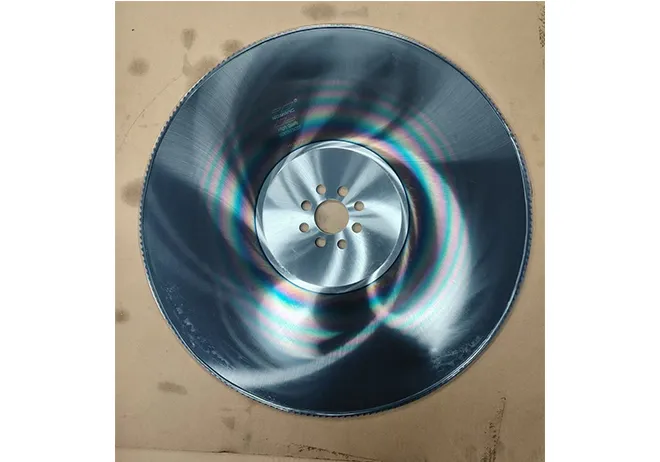
From a business perspective,
cold roll forming is highly cost-effective. The process minimizes waste, as the metal is shaped directly into the final configuration, thus reducing material costs. Furthermore, high production speeds translate to lower labor costs, making it a viable solution for mass production scenarios. Over time, the investment in roll forming machinery can be recovered quickly, especially when producing large volumes of parts.
Cold roll forming is also known for producing components with superior mechanical properties. The process enhances the work hardening of the metal, resulting in products that often have greater strength than those formed through other methods. This increased strength without added weight makes cold roll formed products particularly valuable in industries that demand robust and lightweight components, such as automotive, aerospace, and construction sectors.
what is cold roll forming
Moreover, the environmental advantages of cold roll forming should not be overlooked. Operating at room temperature means that this technique consumes less energy compared to heat-based forming processes. Additionally, the process generates less scrap, contributing to a more sustainable production cycle. As industries strive for greener manufacturing practices, cold roll forming stands out as an appealing option for reducing the carbon footprint of production.
Through firsthand experience, it is evident that the adaptability of cold roll forming is unmatched. It accommodates a variety of metals, including aluminum, stainless steel, and copper, allowing manufacturers to tailor the material properties to specific application needs. The ability to integrate additional features, such as holes, notches, or embosses during the forming process, further enhances the versatility of cold roll forming.
In conclusion, cold roll forming is an essential process in the toolkit of modern manufacturing. Its precision, efficiency, and cost-effectiveness make it a preferred method for producing high-quality, durable components across diverse industries. By leveraging this advanced technique, businesses can not only meet but exceed the expectations of contemporary engineering challenges. From aerospace components to innovative construction materials, cold roll forming delivers on its promise of quality and versatility.
For any organization considering adopting this technology, it's crucial to partner with experienced specialists who understand the nuances of the process. Proper design, tool crafting, and process optimization are vital to unlocking the full potential of cold roll forming. As I've learned through extensive application and study, mastering cold roll forming can significantly contribute to a competitive edge in the manufacturing landscape.