-
Wide Size Range: Capable of producing ERW pipes with diameters from Φ114mm to Φ325mm, covering most large-size industrial demands.
-
Strong Welding Capacity: Equipped with high-power HF induction welding machines, stable for thick-wall materials.
-
Flexible Roll Tooling System: Quick mold change design reduces downtime and supports various pipe sizes.
-
Fully Automated Control: Centralized PLC control with HMI touch screen, easy to operate and adjust.
-
Modular Design: Easy for installation, maintenance, future upgrades, and remote support.
List of Equipment Supply
No.
|
Equipment Name
|
Function Description
|
1
|
Hydraulic Coil Car + Double-Cone Uncoiler
|
Fast coil loading and automatic decoiling with tension control, supports heavy coils.
|
2
|
Shear & Butt Welder
|
Connects two steel strips via automatic shearing and welding to ensure uninterrupted production.
|
3
|
Accumulator
|
Stores steel strip during coil changes to avoid line stoppage and maintain continuity.
|
4
|
Forming Mill (Roughing + Finishing)
|
Gradually bends the flat strip into a round tube; roughing pre-forms, finishing refines.
|
5
|
HF Induction Welder + Cooling System
|
Induction heating and welding of strip edges; water cooling protects equipment and product.
|
6
|
Inner & Outer Burr Removers
|
Removes welding flash to improve pipe appearance and internal smoothness.
|
7
|
Sizing & Straightening Section (with Round-to-Square)
|
Adjusts pipe dimensions, supports square and rectangular tube production.
|
8
|
Flying Saw Cutting System
|
Cuts pipes at preset lengths; supports hot saw, cold saw, or milling cutter.
|
9
|
Output Conveyor + Stacker
|
Automatically aligns, stacks, and discharges finished pipes for further processing.
|
10
|
Centralized Electrical Control (PLC+HMI)
|
Controls the entire line, supports one-button start, fault alarms, and data records.
|
2. BASIC DESIGN DATA
Конструкція запропонованої лінії базується на наступних специфікаціях:
Sizing section and Turkey section usage
Sub-unit
|
Function
|
Sizing Mill
|
Multiple roll stands for radial shaping and sizing with quick-adjust design.
|
Round-to-Square Unit
|
Converts round tubes into square/rectangular ones by changing only sizing rolls.
|
Straightening Device
|
Corrects axial distortion caused by welding/forming to improve straightness and ovality.
|
Surface Polishing Unit
|
Light pressing/polishing rolls improve appearance, suitable for decorative/furniture-grade tubes.
|
Independent Drive System
|
Each stand is driven by variable frequency motors for segmental speed control and easy upgrades.
|
Advantages:
-
Dimensional accuracy within ±0.5mm
-
Fast mold change and format switching
-
Improved product straightness and form
-
Compatible with downstream processes like coating, galvanizing, perforation
-
Suitable for structural, mechanical, construction, transport, and furniture applications
Finishing Auxiliary Equipment Description
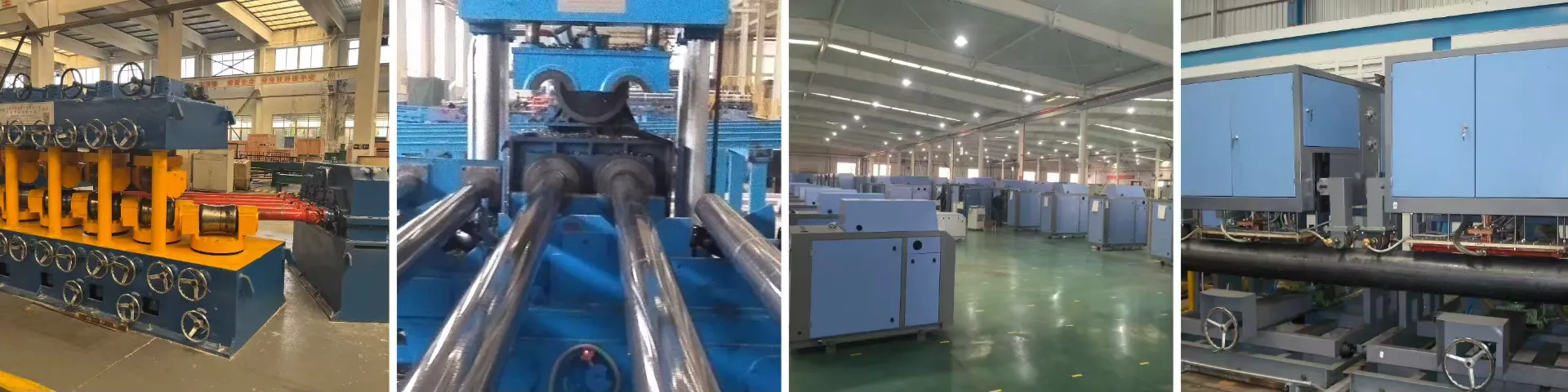
Operating Procedure
-
-
Selection Advice for Customers
-
-
For export or high-end pipe markets, it's recommended to include hydrostatic testing and eddy current inspection systems.
-
For pipe end processing requirements, add the end-facer for precision preparation.
-
Straighteners and bundlers are standard for large-diameter lines and improve finishing automation.
-
All machines can be integrated into a centralized control system for digital traceability and smart management.