-
Milling Cutting Saw Main Unit: This unit is used for precise cutting of pipe materials. It employs high-speed rotating tools to mill and cut pipes accurately, ensuring smooth and high-quality cutting surfaces. It is designed for thick-walled pipes and materials that require precision cutting.
-
Feeding System: Includes conveyor belts, clamping devices, positioning systems, etc., to ensure the pipe material is precisely positioned for cutting.
-
Electrical Control System: Controls cutting speed, cutting position, and other parameters to ensure accurate operation and consistency.
-
Cooling System: Uses cutting fluid to help lower temperatures, reduce friction, and prevent excessive heat buildup during the cutting process. This also helps prolong the life of the tools.
-
Waste Material Handling System: Collects and processes waste materials generated during the cutting process, ensuring a clean and efficient work environment.
-
The pipe material is fed into the cutting area by the feeding system.
-
The milling cutting saw uses rotating cutting tools to mill and cut the pipe material. The process ensures that the cutting surface remains smooth and precise, with minimal burrs.
-
During the cutting process, a cooling fluid is applied to reduce the heat generated by the cutting action and to cool the tools, ensuring consistent performance.
-
After cutting, the finished pipe is conveyed to the next operation stage via the discharge system.
2. BASIC DESIGN DATA
La progettazione della linea proposta si basa sulle seguenti specifiche:
Parameter |
Description |
Pipe Specifications |
Applicable Pipe Diameter: 168mm – 406mm; Wall Thickness: 1.5mm – 16.0mm |
Cutting Speed |
Adjustable based on material and pipe size, typically between 30-100 m/min |
Cutting Precision |
End Face Perpendicularity ±0.2mm, Cutting Smoothness ±0.5mm |
Cutting Tool |
TCT saw blade |
Cooling System |
Cutting fluid spraying system, adjustable fluid flow rate |
Feeding System Speed |
0-20m/min, depending on pipe size and cutting speed |
Electrical Control System |
PLC control system, with speed adjustment, parameter setting, fault diagnosis, etc. |
3. Milling Saw Selection Guide
Item
|
Recommended Range
|
Notes
|
Pipe Diameter Range
|
Φ168 – Φ406mm
|
Match blade size with max pipe size
|
Max Wall Thickness
|
≤16.0mm (Carbon Steel)
|
Best for structural/general-purpose pipes
|
Blade Diameter Options
|
300mm/600mm / 800mm / 1000mm / 1250mm / 1600mm
|
Larger pipes require larger blades
|
Main Motor Power Range
|
55 – 160 kW
|
Depends on pipe size and cutting load
|
Line Cutting Speed
|
80 – 120 m/min
|
Works with servo-driven tracking system
|
Pipe Clamping
|
Pneumatic or hydraulic (double-sided)
|
Ensures stable cutting at high speed
|
Structure Type
|
Double TCT saw blade
|
Dual blade recommended for thick-wall pipes
|
4. Milling Cutting Saw vs. Cold Cutting Saw Performance Comparison
Feature |
Milling Cutting Saw |
Cold Cutting Saw |
Cutting Method |
Uses high-speed rotating tools for milling and cutting |
Uses carbide saw blades for cold cutting |
Cutting Precision |
High precision, maintains smooth end face |
High precision, suitable for thin-walled pipes |
Applicable Materials |
Suitable for medium to thick-walled pipes, especially steel and alloy steel pipes |
Suitable for thin-walled pipes, especially stainless steel and aluminum alloys |
Cutting Speed |
Relatively slow, but suitable for thicker materials and stable cutting |
Relatively fast, especially for high-volume production |
Cutting Surface Quality |
Smooth surface, high precision, but may have minor cutting marks |
Smooth surface, but may have saw-tooth marks |
Tool Wear |
High-speed steel or carbide tools, wear-resistant |
Carbide tools, may wear out quickly at high cutting speeds |
Applicable Pipe Specifications |
Suitable for thick-walled pipes, standard wall thickness pipes |
Suitable for thin-walled pipes |
Post-Cutting Treatment |
Minimal post-processing required |
May require post-processing, such as deburring |
Cooling System |
Uses cutting fluid, maintaining tool life and temperature control |
No cooling fluid used, temperature control may be poorer during cutting |
IL NOSTRO CERTIFICATO
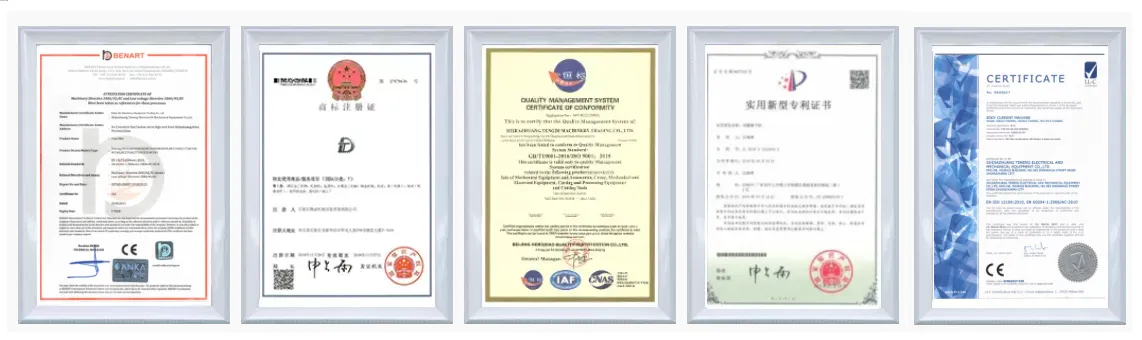