Shear and Butt Welding Machine – Technical Description
1. Application
The shear and butt welding machine is designed for use in ERW tube mill lines. It connects the tail of one steel coil to the head of the next, allowing continuous strip feeding without stopping the production line. This significantly improves efficiency and reduces downtime. It is typically installed before the accumulator section (such as vertical spiral or disc accumulators).
2. Machine Structure
-
Hydraulic Shearing Unit
-
Equipped with upper and lower blades;
-
Powered by hydraulic cylinders;
-
Provides clean, straight cuts across a wide range of strip sizes and thicknesses.
-
Pneumatic Clamping System
-
Left and right side clamping arms;
-
Operated by pneumatic cylinders;
-
Ensures precise alignment and stable positioning of strip ends during welding.
-
TIG Welding Unit
-
Includes TIG welding torch, power supply, and cooling system;
-
Delivers high-quality, low-deformation weld seams.
-
Automatic Torch Travel Mechanism
-
Torch mounted on a guided rail;
-
Travels automatically at a constant speed during welding;
-
Ensures uniform, consistent weld quality.
-
Control System
-
PLC-based with touch screen interface;
-
Full automation of shearing, alignment, and welding steps;
-
Adjustable welding current, travel speed, and other parameters.
3. Features
-
Clean Cuts & Accurate Alignment: Straight, burr-free cuts with minimal mismatch during butt welding.
-
High-Quality Welding: TIG welding ensures smooth, strong, and splash-free weld seams.
-
High Automation: Fully automated process reduces manual labor and ensures repeatability.
-
Material & Time Saving: Minimizes material waste and coil changeover time.
-
Easy Maintenance: Compact structure with accessible components for easy servicing.
4. Applicable Scope
-
Material Types: Carbon steel, stainless steel, galvanized steel strips.
-
Largeur de la bande: Customizable, typically from 300 to 1600mm.
-
Thickness Range: 0.8mm to 6.0mm (depending on cutting and welding specs).
-
Applicable Lines: ERW tube mills, slitting lines, cold roll forming lines, etc.
5. Frequently Asked Questions (FAQ)
Q1: Does the shear and butt welding machine affect weld quality?
A1: No. The TIG welding system delivers stable, high-quality welds. The automatic torch travel ensures uniform bead formation, suitable for further forming and HF welding processes.
Q2: Can it weld different materials together?
A2: Yes, but it is recommended to weld same or similar materials (with matching melting points) to ensure optimal joint strength. Parameters can be adjusted for dissimilar materials.
Q3: Is manual operation required during coil change?
A3: No manual welding is needed. Operators only position the new strip; the system automatically performs shearing, alignment, and welding.
Q4: Are TIG consumables and operating costs high?
A4: TIG welding requires argon gas and tungsten electrodes, but it ensures excellent welding quality. For automated production lines, its stability and low rework rates justify the cost.
Q5: Can it be retrofitted to existing production lines?
A5: Yes. Custom solutions are available to match your current line layout, accumulator type, and process requirements.
EQUIPEMENT DE RELATION
Nous fournissons tout l'équipement pour la section d'entrée du laminoir à tubes :
Voiture à bobine
Dérouleur à tête simple et double et dérouleur hydraulique et pneumatique
Bras d'éplucheur et de maintien du rouleau
Machine à aplatir
Cisailleuse et soudeuse bout à bout automatique et semi-automatique
Vertical Cage Accumulator & Horizontal Loop Accumulator & Landing Horizontal Spiral Loop Accumulator

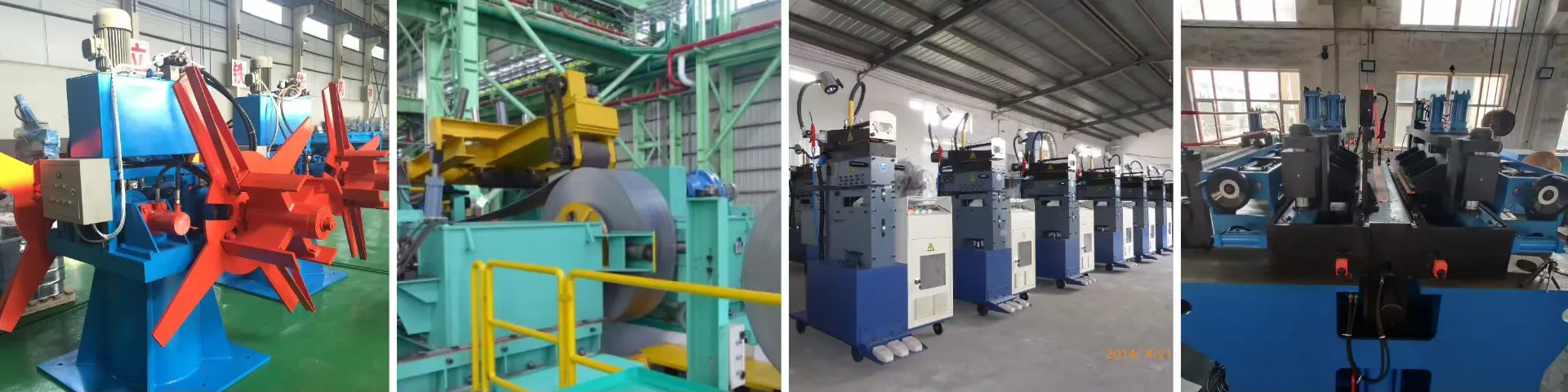
NOTRE SERVICE
Pourquoi nous choisir?
Technologie de pointe, qualité fiable, excellent service !
Conception optimisée, sélection de matériaux de haute qualité !
Garantie du processus de traitement thermique !
Engrenage conique hélicoïdal, accouplement à tambour et cémentation.
Trempe des dents d'engrenages.
Système d'entraînement stable, efficace et portable avec moins de bruit.
Haute précision, résistance à l'usure et longue durée de vie des rouleaux.
Tous les tours mécaniques, les rainures de clavette sont positionnés et fraisés par CNC.
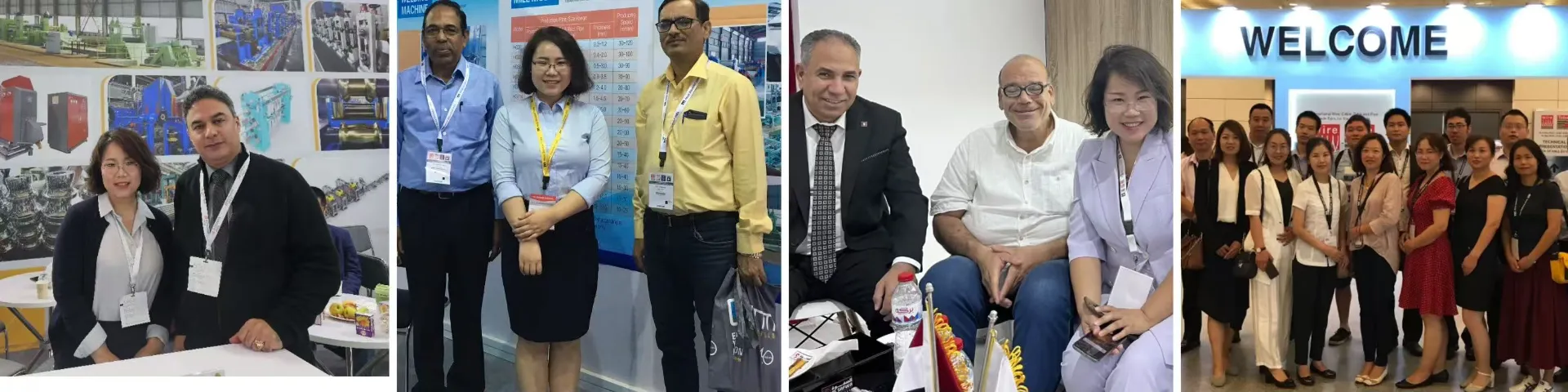