Shear and Butt Welding Machine – Technical Description
1. Application
The shear and butt welding machine is designed for use in ERW tube mill lines. It connects the tail of one steel coil to the head of the next, allowing continuous strip feeding without stopping the production line. This significantly improves efficiency and reduces downtime. It is typically installed before the accumulator section (such as vertical spiral or disc accumulators).
2. Machine Structure
-
Hydraulic Shearing Unit
-
Equipped with upper and lower blades;
-
Powered by hydraulic cylinders;
-
Provides clean, straight cuts across a wide range of strip sizes and thicknesses.
-
Pneumatic Clamping System
-
Left and right side clamping arms;
-
Operated by pneumatic cylinders;
-
Ensures precise alignment and stable positioning of strip ends during welding.
-
TIG Welding Unit
-
Includes TIG welding torch, power supply, and cooling system;
-
Delivers high-quality, low-deformation weld seams.
-
Automatic Torch Travel Mechanism
-
Torch mounted on a guided rail;
-
Travels automatically at a constant speed during welding;
-
Ensures uniform, consistent weld quality.
-
Control System
-
PLC-based with touch screen interface;
-
Full automation of shearing, alignment, and welding steps;
-
Adjustable welding current, travel speed, and other parameters.
3. Features
-
Clean Cuts & Accurate Alignment: Straight, burr-free cuts with minimal mismatch during butt welding.
-
High-Quality Welding: TIG welding ensures smooth, strong, and splash-free weld seams.
-
High Automation: Fully automated process reduces manual labor and ensures repeatability.
-
Material & Time Saving: Minimizes material waste and coil changeover time.
-
Easy Maintenance: Compact structure with accessible components for easy servicing.
4. Applicable Scope
-
Material Types: Carbon steel, stainless steel, galvanized steel strips.
-
Strip Width: Customizable, typically from 300 to 1600mm.
-
Thickness Range: 0.8mm to 6.0mm (depending on cutting and welding specs).
-
Applicable Lines: ERW tube mills, slitting lines, cold roll forming lines, etc.
5. Frequently Asked Questions (FAQ)
Q1: Does the shear and butt welding machine affect weld quality?
A1: No. The TIG welding system delivers stable, high-quality welds. The automatic torch travel ensures uniform bead formation, suitable for further forming and HF welding processes.
Q2: Can it weld different materials together?
A2: Yes, but it is recommended to weld same or similar materials (with matching melting points) to ensure optimal joint strength. Parameters can be adjusted for dissimilar materials.
Q3: Is manual operation required during coil change?
A3: No manual welding is needed. Operators only position the new strip; the system automatically performs shearing, alignment, and welding.
Q4: Are TIG consumables and operating costs high?
A4: TIG welding requires argon gas and tungsten electrodes, but it ensures excellent welding quality. For automated production lines, its stability and low rework rates justify the cost.
Q5: Can it be retrofitted to existing production lines?
A5: Yes. Custom solutions are available to match your current line layout, accumulator type, and process requirements.
RELATION EQUIPMENT
We provides all equipment to tube mill entry section:
Coil Car
Single And Double Heads Un-coiler & Hydraulic And Pneumatic Un-coiler
Peeler and hold down roll arm
Flattening Machine
Automatic and Semi Auto Shearer & Butt Welder
Vertical Cage Accumulator & Horizontal Loop Accumulator & Landing Horizontal Spiral Loop Accumulator

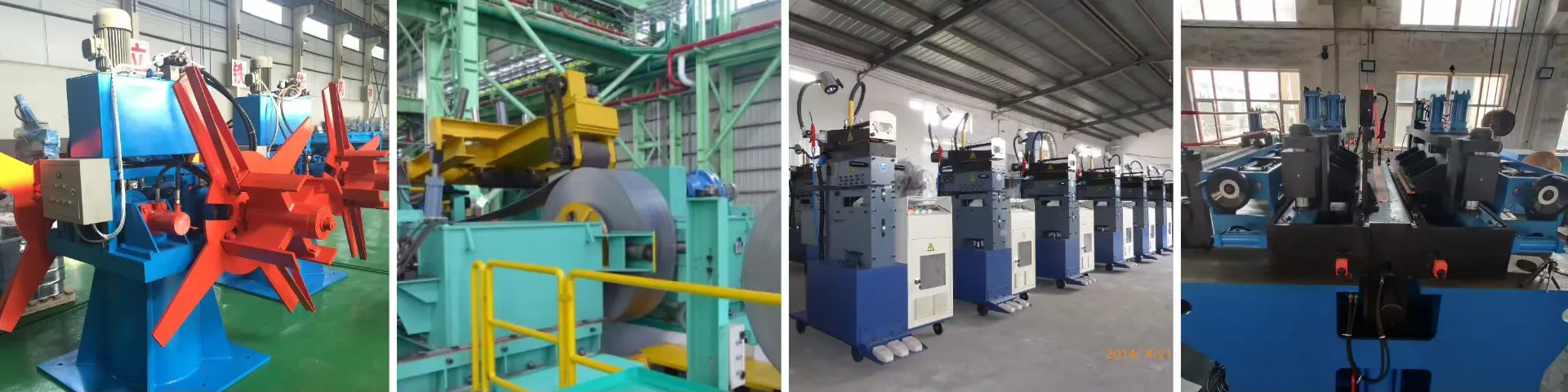
OUR SERVICE
Why Choose Us?
Leading Technology, Reliable Quality, Excellent Service!
Optimized Design, High quality material select!
Heat treatment process guarantee!
Spiral bevel gear, drum gear coupling and carburization.
Gear teeth quenching.
Driven system stable, efficient and wearable with lower noise.
High precision wear resisting and Long life of rollers.
All the machine Lathes, Key Grooves are positioned and Milled by CNC.
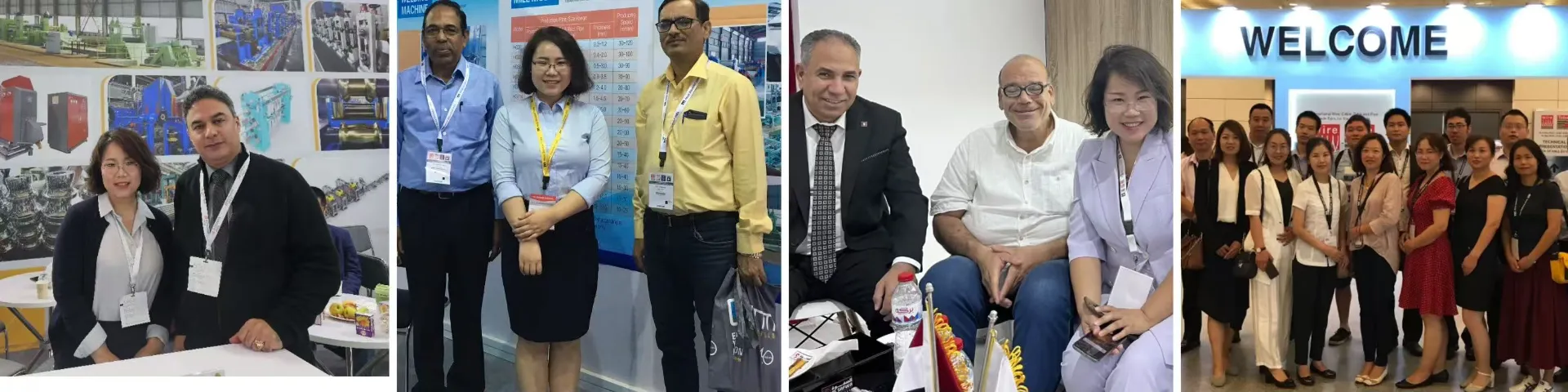