Solar Panel Frame Roll Forming Machine (Carbon Steel Type)
1. Introduction
This roll forming line is engineered for manufacturing carbon steel frames used in photovoltaic (PV) solar panels. Designed for stability and efficiency, the machine automates punching, forming, and cutting in a continuous process, allowing for high-precision frame production with minimal material waste.
This model is optimized for long-run production with programmable control and real-time diagnostics.
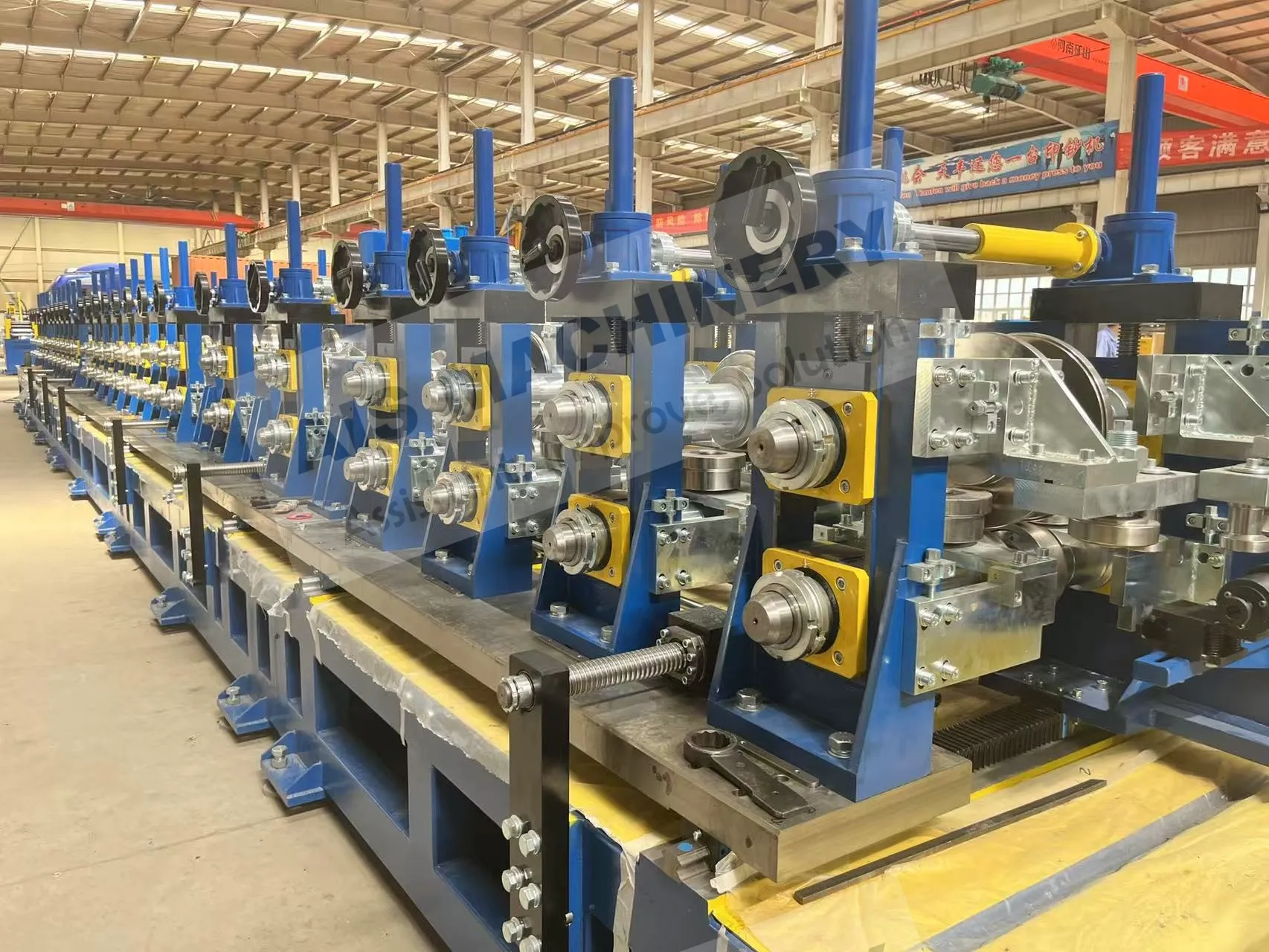
2. Machine Composition
The system is composed of the following modules:
-
Manual Decoiler or Hydraulic Uncoiler
-
Feeding and Leveling System
-
Precision Servo Punching Station
-
Main Roll Forming Section
-
Servo Flying Shear Cut-Off Unit
-
Runout Table and Optional Auto Stacker
-
Centralized Electrical Control System (PLC + HMI)
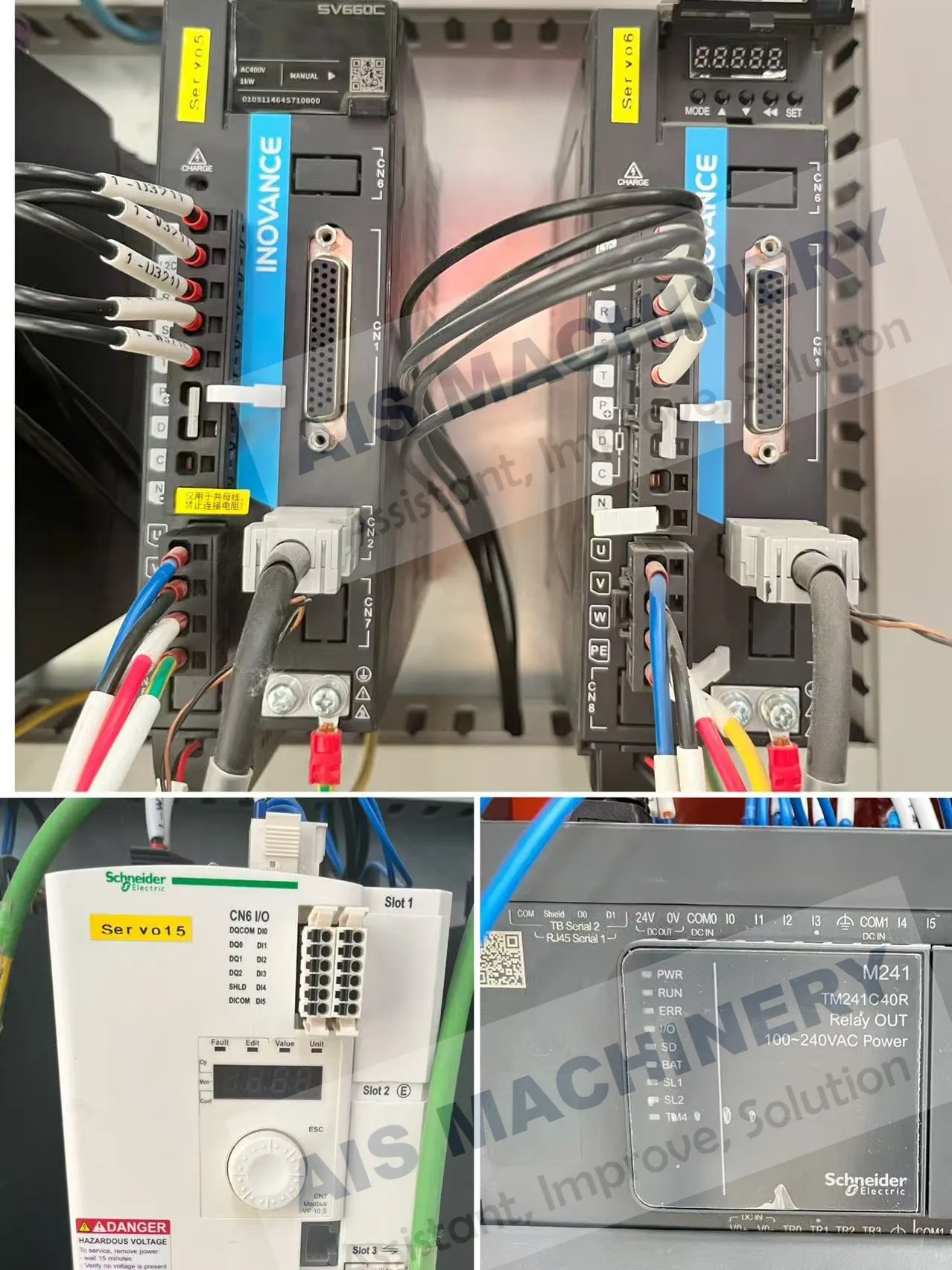
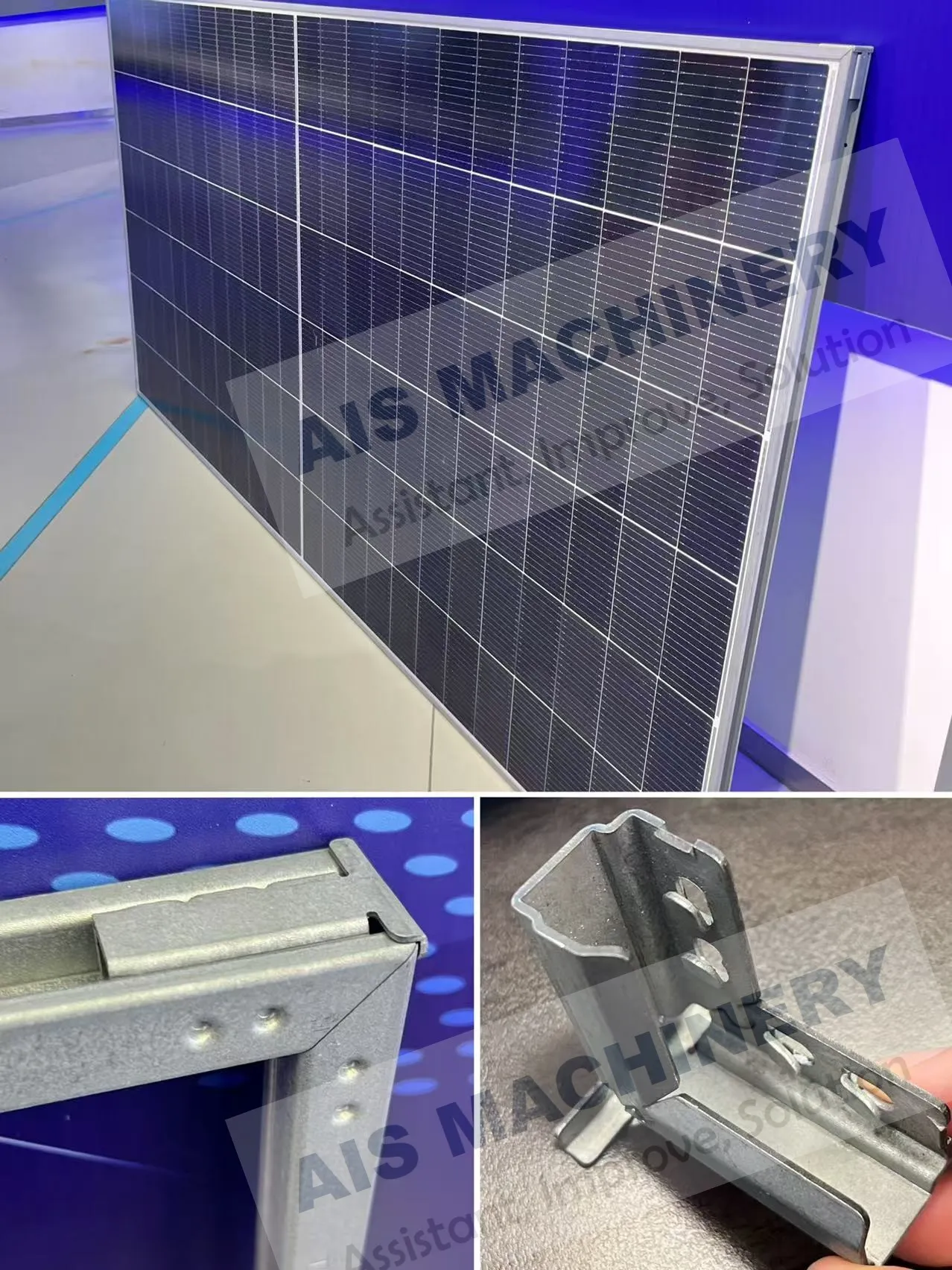
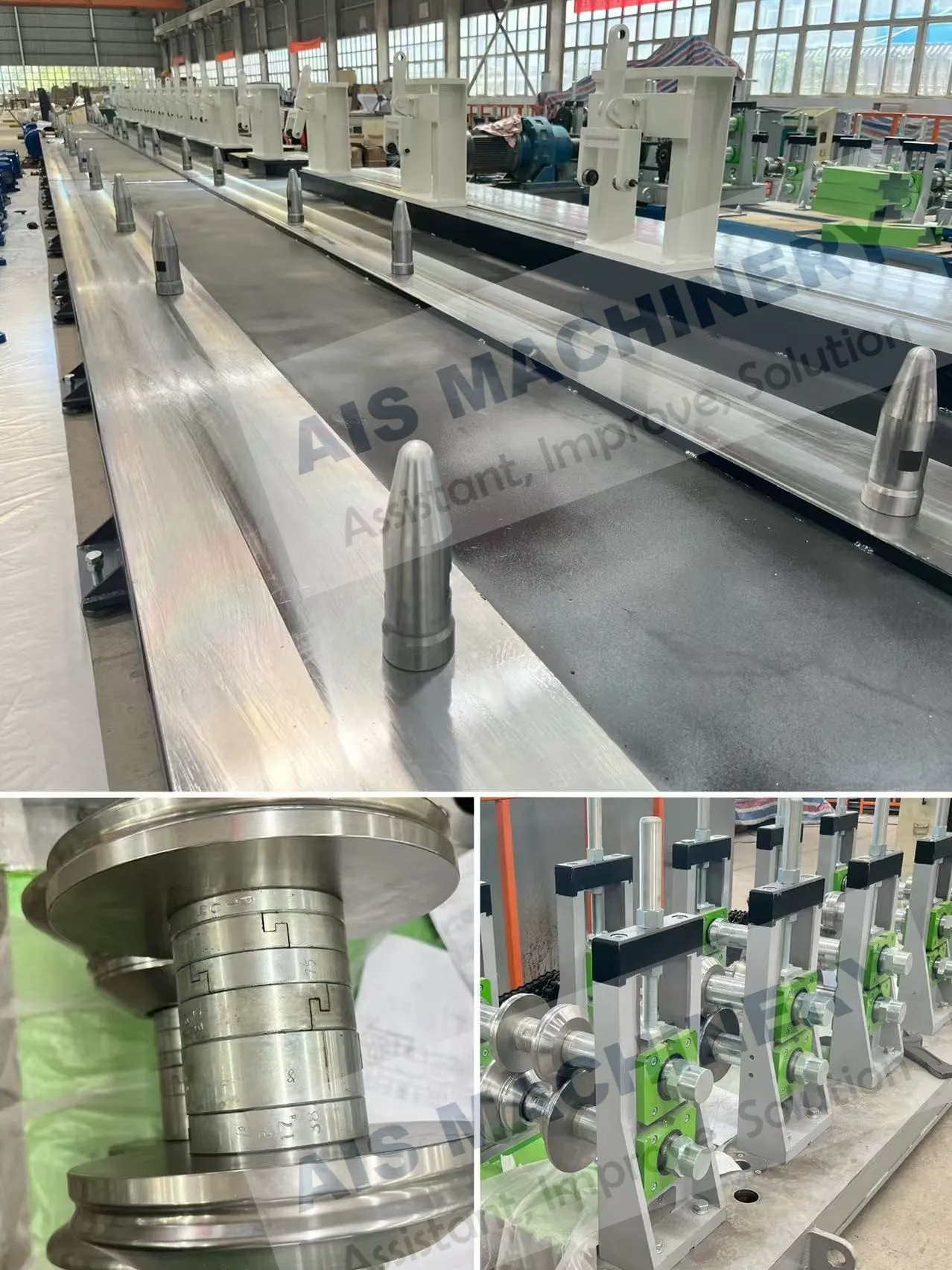
3. Technical Data
Parameter |
Specification |
Frame Material |
Cold rolled carbon steel, galvanized steel |
Material Width |
45 – 100 mm |
Material Thickness |
0.8 – 2.0 mm |
Production Speed |
Up to 15 meters per minute |
Forming Stations |
14 – 20 steps (customizable) |
Cutting Tolerance |
±0.3 mm |
Punching Accuracy |
±0.5 mm |
Control System |
Siemens PLC, touch HMI, encoder feedback |
Required Power Supply |
380V, 50Hz, 3-phase |
4. Operating Procedure
▶️ Before You Start
-
Check power connection, oil level in hydraulic system, and air pressure.
-
Ensure the punching mold and cutting blade are clean and firmly secured.
-
Load the steel coil on the uncoiler and lock with safety clamps.
▶️ Startup Process
-
System Boot
-
Parameter Input via HMI
-
Input length of frame, punching positions, and number of holes.
-
Set the batch quantity and material thickness.
-
Load or recall saved profile data if applicable.
-
Material Feeding
-
Production Mode
-
Switch to “Auto Run”.
-
Monitor the HMI screen for live speed, punch counts, and cut count.
-
Inspect first 2–3 frames for dimensional accuracy.
▶️ Stopping & Changeover
-
Press “Stop” and wait for the current piece to finish cutting.
-
Change punching dies or adjust rollers if switching frame types.
-
Use jog mode to test feed before resuming auto production.
5. Routine Maintenance
Task |
Frequency |
Notes |
Clean roll surfaces |
Daily |
Use anti-rust oil |
Check punching die wear |
Weekly |
Replace if edge dull |
Lubricate forming bearings |
Every 2 days |
Use light-grade machine oil |
Inspect sensors & cables |
Weekly |
Check for wear or disconnection |
Back up PLC data |
Monthly |
Via USB port on HMI |
6. Troubleshooting Guide
Symptom |
Possible Cause |
Solution |
Frame length deviation |
Encoder loose / wrong data |
Recalibrate encoder |
Punch misalignment |
Servo lag or mold shift |
Reposition mold and reset zero |
Uneven frame shape |
Roller misadjusted |
Re-level forming station |
Material jam in cutter |
Blade worn or too slow |
Replace blade, adjust servo timing |
7. Frequently Asked Questions (FAQ)
Q: Is carbon steel strong enough for outdoor frames?
A: Yes. With proper galvanization or powder coating, carbon steel frames offer excellent strength and corrosion resistance at a much lower cost than aluminum.
Q: Can one machine make different sizes?
A: Absolutely. Frame length, hole positions, and even roll gaps can be adjusted via PLC. Some wider profiles may need partial tool change.
Q: What is the estimated tool life?
A: Punching dies typically last 80,000–120,000 cycles depending on material. Cutting blades may last 30,000–50,000 cuts with proper lubrication.
Q: Can I integrate a stacker later?
A: Yes. The output section includes optional ports and logic for integration with auto stackers or robotic arms.
8. Safety Instructions
-
Never place hands near the roll station during operation.
-
Always disconnect power before adjusting tooling.
-
Emergency stops are located at the entry and exit ends.
-
Wear gloves and safety glasses when changing dies.
This strip in the profiling stands progressively transforms towards its final shape.This process respects the mechanical and characteristic stresses of the metal and allows the use of multiple grades of steels.Two horizontal shafts of each head are controlled by the motor of the machine, which ensures a regular drive of the strip.During the cold roll forming, operations such as punching holes, stamping logo, can be done online.
Then, the final metal section is cut by hydraulic servo cutoff machine to the desired length.
1.What is a roll forming machine used for?
Cold roll forming machines are used in a variety of industries, including construction, automotive, aerospace, and manufacturing. They are highly automated and can produce high-quality products at a high rate of speed, making them a popular choice for mass production.
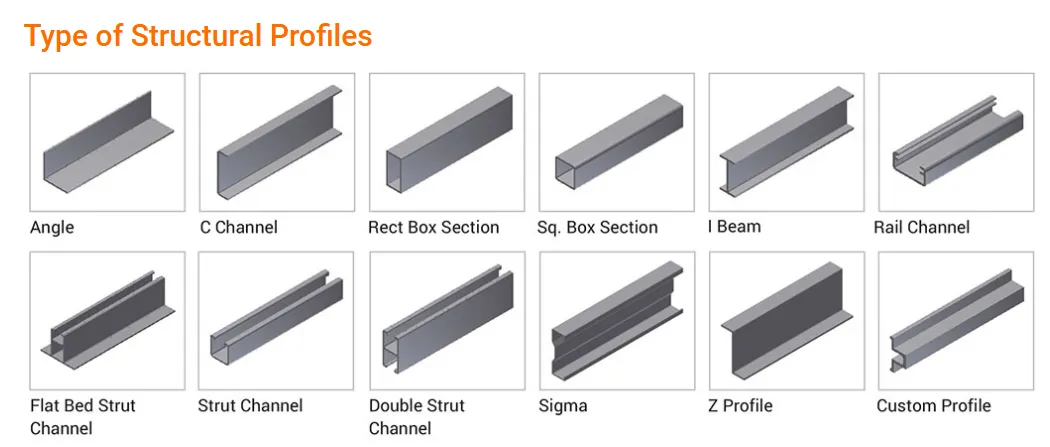
4. The technical flow of the production line
{Steel Tape}→ Uncoiler →Strip-head Cutter and welder→Spiral accumulator→Forming section →Hole punching device→Hydraulic servo driven cutoff→→ Run-out table
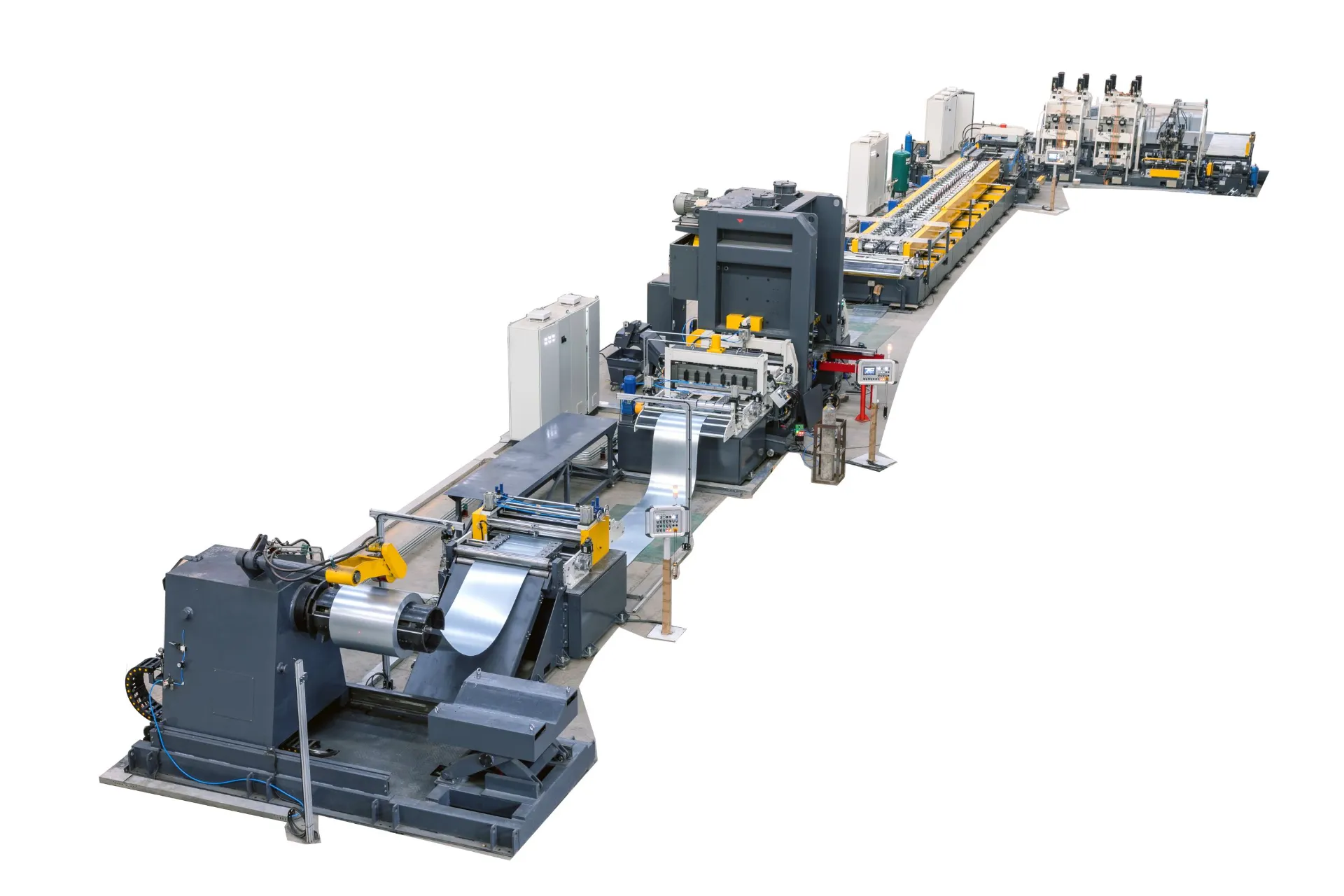
RELATION EQUIPMENT
We provides all equipment to tube mill entry section:
Coil Car
Single And Double Heads Un-coiler & Hydraulic And Pneumatic Un-coiler
Peeler and hold down roll arm
Flattening Machine
Automatic and Semi Auto Shearer & Butt Welder
Vertical Cage Accumulator & Horizontal Loop Accumulator & Landing Horizontal Spiral Loop Accumulator
TUBE MILL FINISHING SECTION
We provides all equipment to tube mill Finishing section:
1. Eddy current machine
2. Seam annealing machine
3. Straightener machine
4. Chamfer and end facer machine
5. Hydro Tester machine
6. Threading machine
7. Painting and oil machine
8. Automatic bundle and package machine
9. Drilling machine
SPARE PARTS TO CHOOSE
Our Spare Parts Apply:
1. Roller, Mould, Cr12, Cr12Mov material, D2,D3 material
2. Ferrite, Impeder, Fiberglass tube
3. HSS saw blades, TCT Saw blades, Friction saw blades
4. OD burr remove inserts, ID burr remover inserts
5. HF welder Induction Coil and other HF welder spare parts
6. Copper tube for induction Coil, PTFE pipe for Induction Coil
7. Mosfet, Boards
8. Steel pipe Strapping machine
9. Zinc Spray Machine, Zinc wire, Zinc spray gun
OUR CERTIFICATE
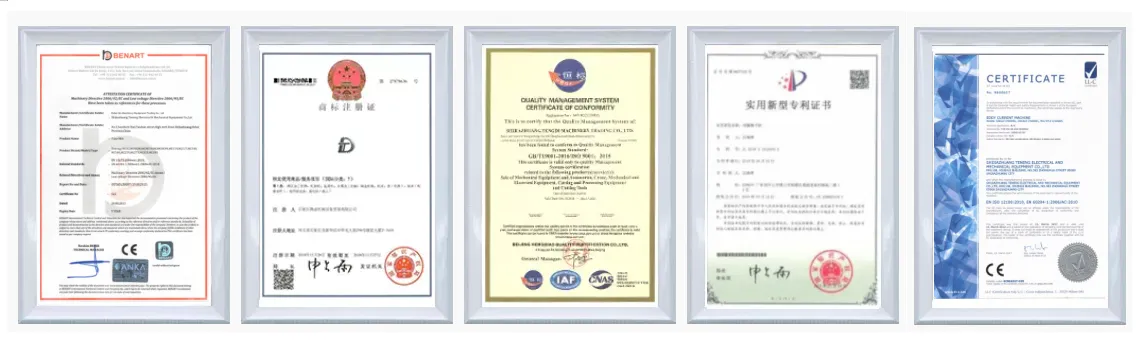
OUR SERVICE
Why Choose Us?
Leading Technology, Reliable Quality, Excellent Service!
Optimized Design, High quality material select!
Heat treatment process guarantee!
Spiral bevel gear, drum gear coupling and carburization.
Gear teeth quenching.
Driven system stable, efficient and wearable with lower noise.
High precision wear resisting and Long life of rollers.
All the machine Lathes, Key Grooves are positioned and Milled by CNC.
Our Service
Pre-sale service
1. We can provide machine running videos for reference
2. We will recommend the most suitable equipment according to the needs of customers
3. We can provide the layout of the factory
4. We welcome customers to visit our factory
After-sales service
1.We will delivery the machine and provide the documents on time to make sure you can get the machine quickly
2.When you finish the Preparation conditions, Our fast and professional aftersales service engineer team will go to your factory to install the machine, give you the operating manual, And train your employee until they can operate the machine well.
3.We provide one year warranty and life-long technical support.
4.Well-trained & experienced staff are to answer all your inquiries in English and Chinese
5 .24 hours for engineer response.
6.Your business relationship with us will be confidential to any third party.
Quality Control
We have the single quality department, that make sure the material of the raw materials is good, and ensure the machine running smoothly.