Warehouse Storage Rack Roll Forming Machine
1. Introduction
The Warehouse Pallet Rack Roll Forming Machine is designed for the high-efficiency production of upright frames, step beams, and horizontal braces used in industrial shelving and storage systems. It is suitable for mass production of roll-formed components with consistent dimensions, high strength, and minimal material waste.
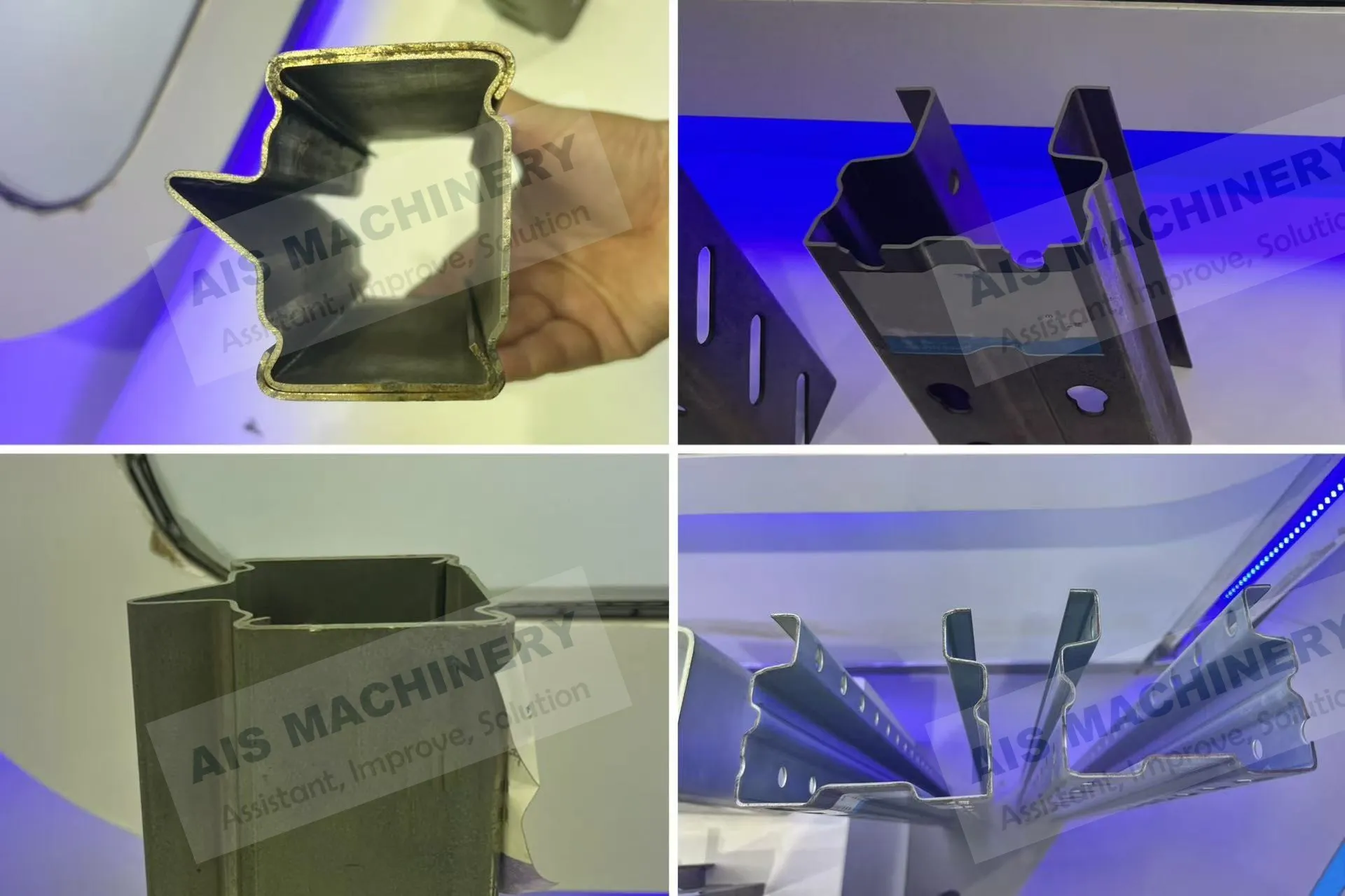
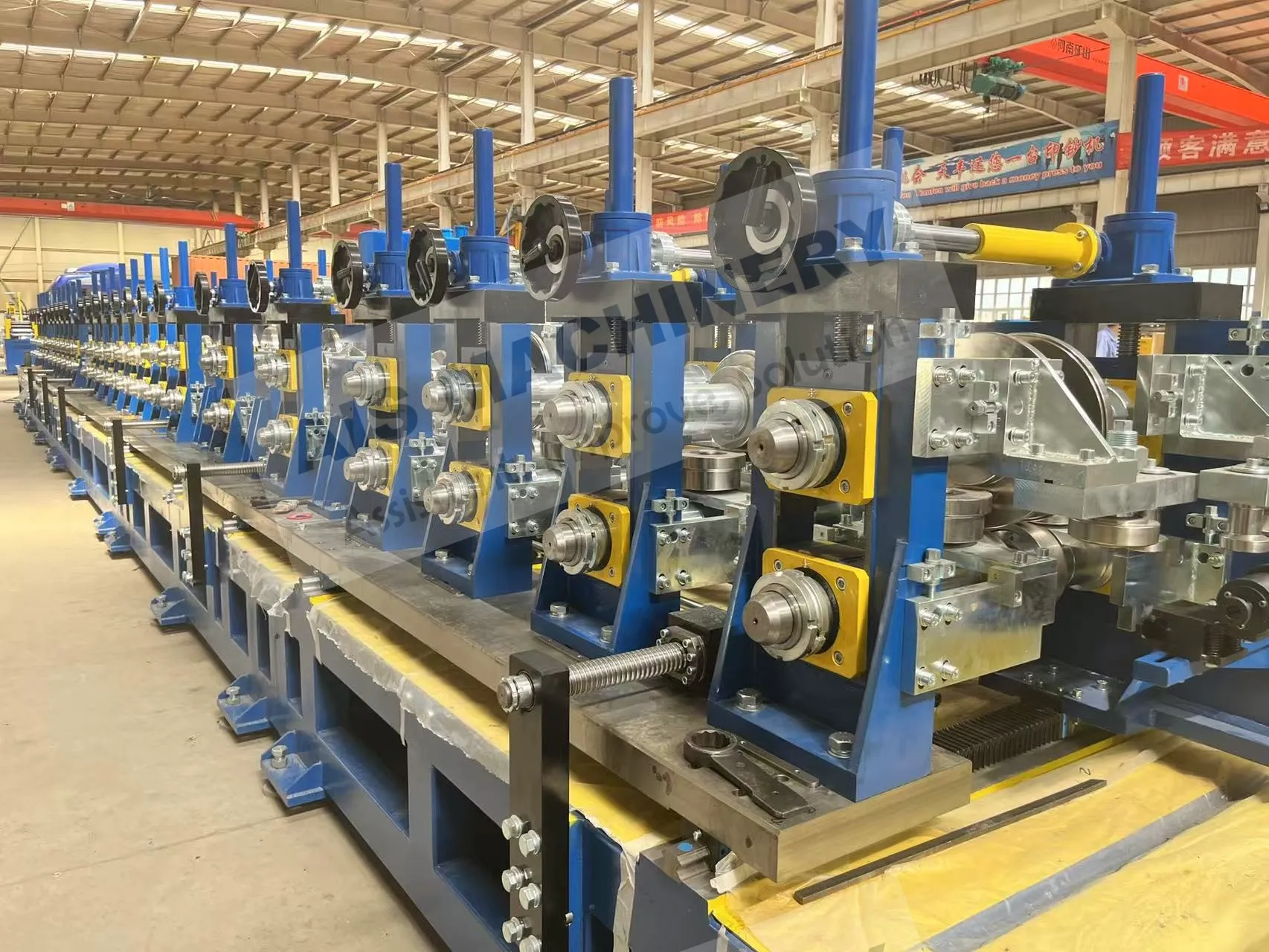
2. Technical Specifications
Item |
Specification |
Raw Material |
Cold-rolled steel / Galvanized steel |
Material Thickness |
1.5–2.5 mm (customizable) |
Material Width |
100–500 mm (based on profile) |
Forming Stations |
16–28 stations (depending on profile) |
Forming Speed |
10–15 m/min (with punching) |
Roller Material |
GCr15 steel, heat treated, chromed |
Drive System |
Gearbox drive / Chain drive |
Cutting Type |
Servo driven following cutoff |
PLC Control |
Siemens /China brand |
Voltage |
380V / 50Hz / 3 Phase (customizable) |
\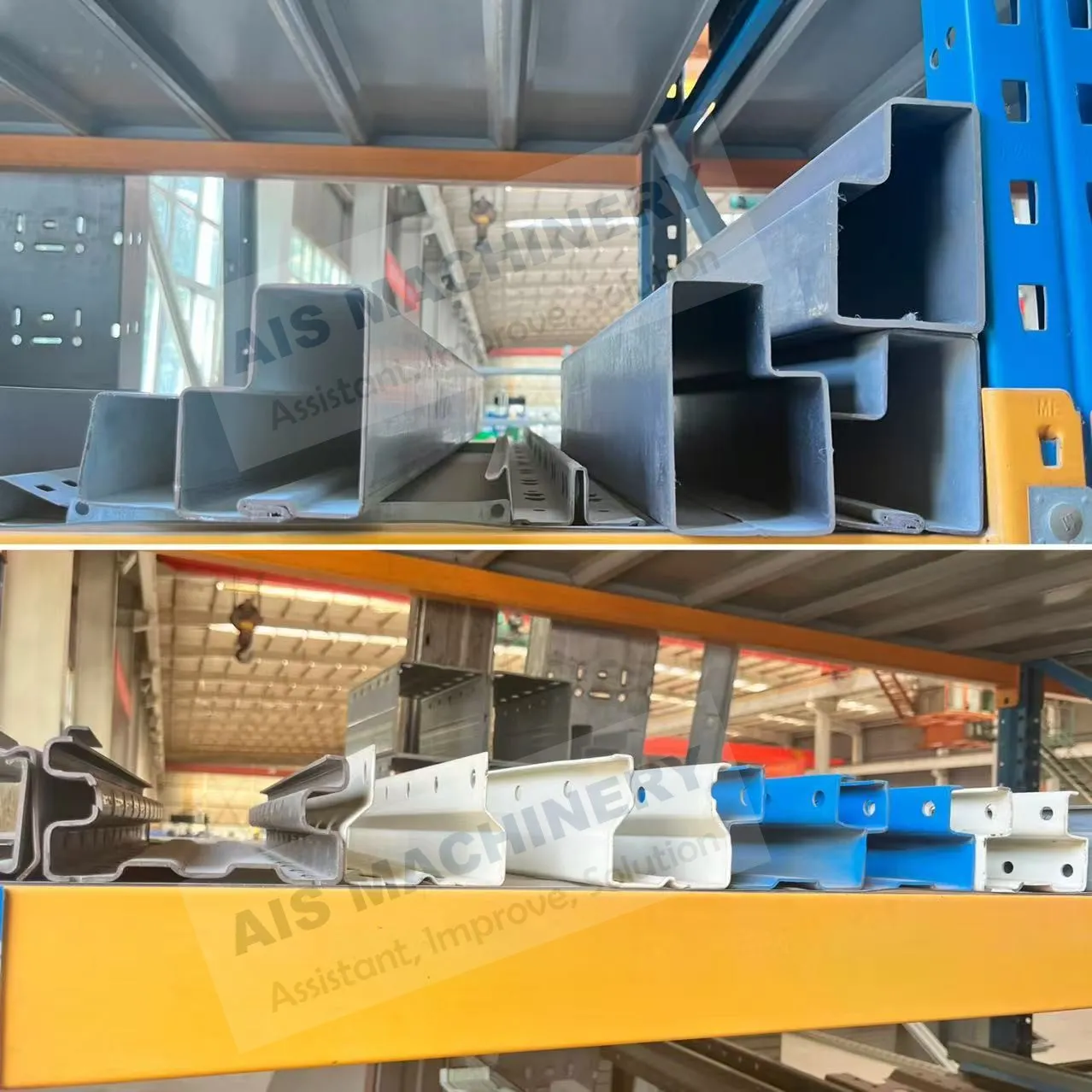
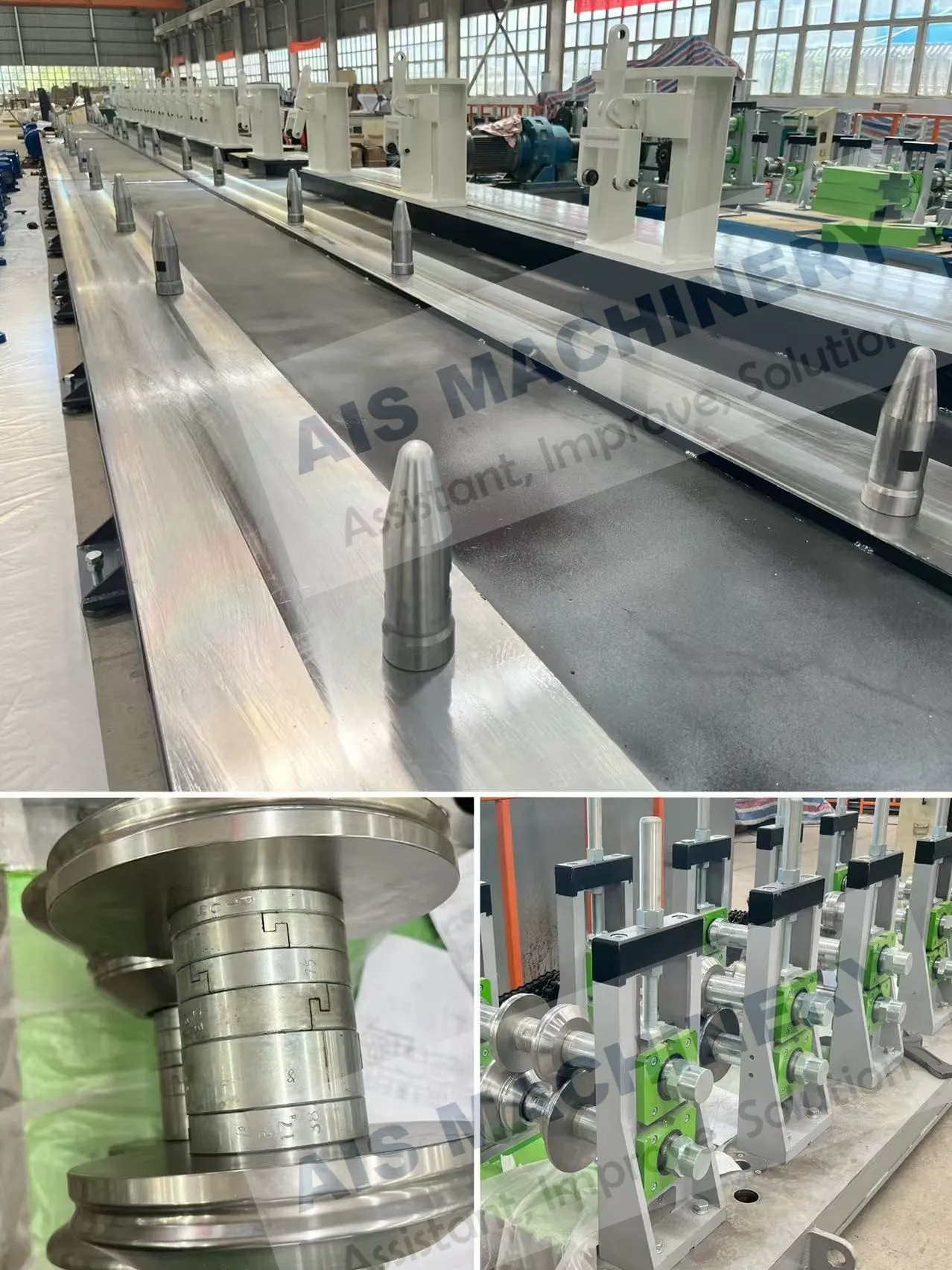
3. Machine Composition
-
Uncoiler – Manual or hydraulic type, holds coil steel
-
Feeding & Leveling Unit – Ensures smooth, aligned feeding
-
Servo Punching Unit – Customized punching dies for beam holes or upright slots
-
Roll Forming System – Precision rollers for forming beam/upright shape
-
Cutting Unit – Hydraulic or flying shear, length-controlled
-
Output Table – Collects finished products
-
Control Cabinet (PLC) – Full automation, touch screen interface
-
Optional Devices: Pre-punching, notching, embossing, stacking systems
4. Application Scenarios
-
Industrial warehouse storage systems
-
Supermarket shelving
-
Cold storage rack systems
-
Logistic centers
-
Heavy-duty pallet racking
5. Production Flow
6. Operation Instructions
-
Load the steel coil on the uncoiler.
-
Adjust the leveling rollers to match thickness.
-
Load the required punching die (if needed).
-
Select product type and set parameters on PLC.
-
Run dry test (no material) to ensure alignment.
-
Feed steel into rollers and start production.
-
Monitor the forming and cutting accuracy during the run.
-
After production, clean and lubricate the rollers.
7. FAQs
Q1: Can it produce both uprights and beams on one line?
A1: Normally not; separate roller sets or machines are used for different profiles, but modular roller replacement systems are available.
Q2: How long does it take to change a profile?
A2: With manual roller change: 3–5 hours. With quick-change cassette system: under 1 hour.
Q3: What kind of punching is supported?
A3: Both inline servo punching and hydraulic punching are supported, depending on production requirements.
Q4: How accurate is the cutting length?
A4: ±1.0 mm with PLC length control and encoder system.
Q5: Is remote support available?
A5: Yes, the PLC supports remote troubleshooting via internet (if equipped).
8. Maintenance Tips
-
Regularly clean rollers and apply anti-rust oil
-
Check hydraulic oil level and filters monthly
-
Tighten all bolts and drive chains weekly
-
Inspect electric control cabinet for overheating
8. Safety Instructions
-
Never place hands near the roll station during operation.
-
Always disconnect power before adjusting tooling.
-
Emergency stops are located at the entry and exit ends.
-
Wear gloves and safety glasses when changing dies.
This strip in the profiling stands progressively transforms towards its final shape.This process respects the mechanical and characteristic stresses of the metal and allows the use of multiple grades of steels.Two horizontal shafts of each head are controlled by the motor of the machine, which ensures a regular drive of the strip.During the cold roll forming, operations such as punching holes, stamping logo, can be done online.
Then, the final metal section is cut by hydraulic servo cutoff machine to the desired length.
1.What is a roll forming machine used for?
Cold roll forming machines are used in a variety of industries, including construction, automotive, aerospace, and manufacturing. They are highly automated and can produce high-quality products at a high rate of speed, making them a popular choice for mass production.
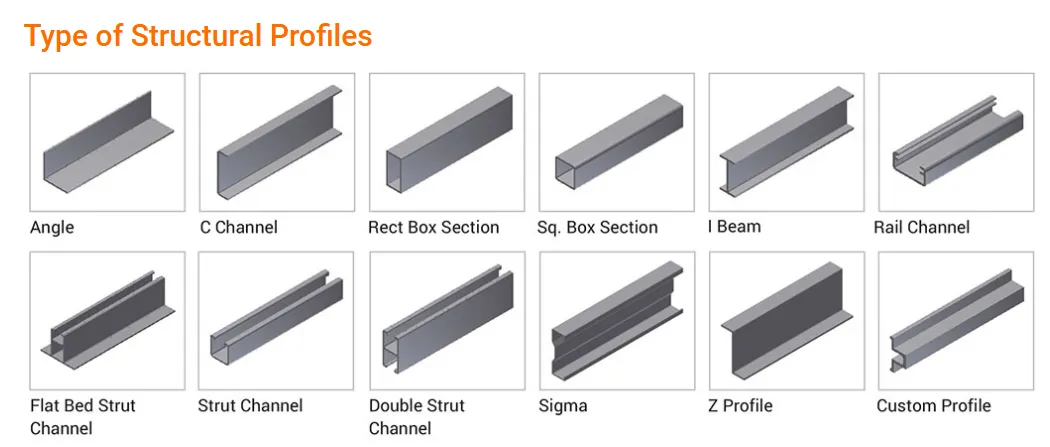
RELATION EQUIPMENT
We provides all equipment to tube mill entry section:
Coil Car
Single And Double Heads Un-coiler & Hydraulic And Pneumatic Un-coiler
Peeler and hold down roll arm
Flattening Machine
Automatic and Semi Auto Shearer & Butt Welder
Vertical Cage Accumulator & Horizontal Loop Accumulator & Landing Horizontal Spiral Loop Accumulator
TUBE MILL FINISHING SECTION
We provides all equipment to tube mill Finishing section:
1. Eddy current machine
2. Seam annealing machine
3. Straightener machine
4. Chamfer and end facer machine
5. Hydro Tester machine
6. Threading machine
7. Painting and oil machine
8. Automatic bundle and package machine
9. Drilling machine
SPARE PARTS TO CHOOSE
Our Spare Parts Apply:
1. Roller, Mould, Cr12, Cr12Mov material, D2,D3 material
2. Ferrite, Impeder, Fiberglass tube
3. HSS saw blades, TCT Saw blades, Friction saw blades
4. OD burr remove inserts, ID burr remover inserts
5. HF welder Induction Coil and other HF welder spare parts
6. Copper tube for induction Coil, PTFE pipe for Induction Coil
7. Mosfet, Boards
8. Steel pipe Strapping machine
9. Zinc Spray Machine, Zinc wire, Zinc spray gun
OUR CERTIFICATE
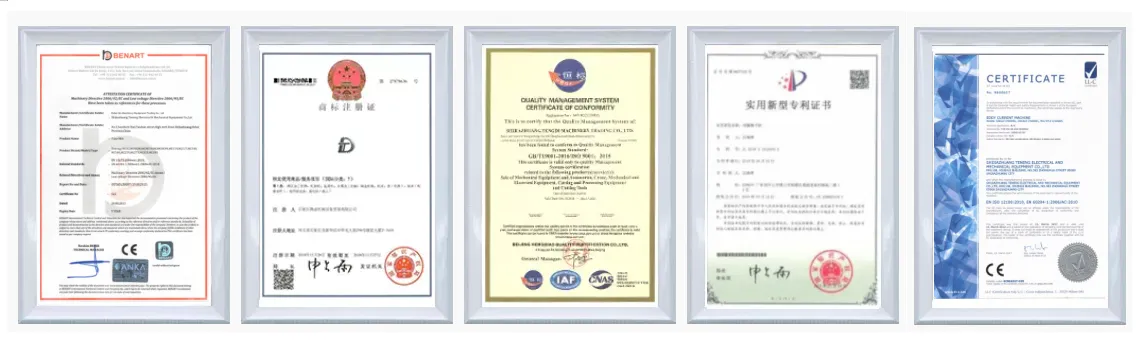
OUR SERVICE
Why Choose Us?
Leading Technology, Reliable Quality, Excellent Service!
Optimized Design, High quality material select!
Heat treatment process guarantee!
Spiral bevel gear, drum gear coupling and carburization.
Gear teeth quenching.
Driven system stable, efficient and wearable with lower noise.
High precision wear resisting and Long life of rollers.
All the machine Lathes, Key Grooves are positioned and Milled by CNC.
Our Service
Pre-sale service
1. We can provide machine running videos for reference
2. We will recommend the most suitable equipment according to the needs of customers
3. We can provide the layout of the factory
4. We welcome customers to visit our factory
After-sales service
1.We will delivery the machine and provide the documents on time to make sure you can get the machine quickly
2.When you finish the Preparation conditions, Our fast and professional aftersales service engineer team will go to your factory to install the machine, give you the operating manual, And train your employee until they can operate the machine well.
3.We provide one year warranty and life-long technical support.
4.Well-trained & experienced staff are to answer all your inquiries in English and Chinese
5 .24 hours for engineer response.
6.Your business relationship with us will be confidential to any third party.
Quality Control
We have the single quality department, that make sure the material of the raw materials is good, and ensure the machine running smoothly.