In the evolving landscape of industrial applications, the welded tube mill stands as a crucial component in the manufacturing and fabrication industries. Known for its versatility and efficiency, it plays a vital role in the production of high-quality metal tubes and pipes, which are essential across various sectors such as construction, automotive, and energy.
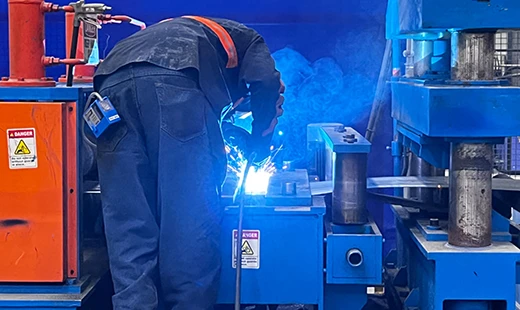
Experience from seasoned industry professionals highlights that the welded tube mill is an indispensable tool for producing tubes that meet exact specifications and quality standards. Operators with years of hands-on experience emphasize the importance of precision and calibration in the operation of these mills. Misalignment or incorrect settings can lead to significant material waste and production downtime, underscoring the necessity for skilled technicians who can ensure optimal performance.
From an expertise standpoint, mastering the welded tube mill requires a deep understanding of metallurgy and material science. Each metal type, whether steel, stainless steel, or aluminum,
reacts differently under the conditions imposed by a tube mill. The control of variables such as temperature, pressure, and welding speed are critical to maintain the integrity of the tube’s structure. Innovations in welding techniques, such as high-frequency induction welding and laser welding, have transformed production efficiency, offering higher precision and reduced energy consumption.
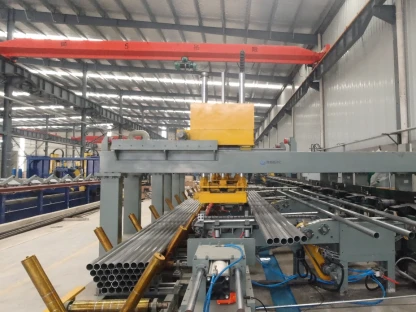
Authoritativeness in this domain is bolstered by adhering to international standards and certifications. The American Society for Testing and Materials (ASTM) and the International Organization for Standardization (ISO) provide comprehensive guidelines and benchmarks for tube quality and production processes. Compliance with such standards not only ensures product reliability but also enhances a company’s reputation in global markets. Leading manufacturers often invest in the latest technology and training to align with these standards, positioning themselves as trustworthy suppliers.
welded tube mill
Trustworthiness in the welded tube mill sector goes beyond technical expertise and aligns with an unwavering commitment to quality and customer satisfaction. Clients depend on manufacturers for consistent and reliable products that withstand rigorous application requirements. Transparency in process documentation and traceability in production batches is critical, allowing for accountability and swift resolution in the event of discrepancies.
The future of welded tube mills seems promising, with advancements in automation and smart manufacturing technologies. Industry 4.0 integration facilitates real-time monitoring and data analytics, optimizing production lines and predictive maintenance. This shift not only enhances productivity but also reduces operational costs, marking a pivotal transformation in the industry.
In summary, the welded tube mill represents a fusion of technical prowess and industrial innovation. Its role in modern manufacturing underscores the importance of experience, technical expertise, authoritative standards, and trustworthy practices. As industries continue to evolve, the demand for precision-engineered tubes and pipes will drive further advancements in tube mill technologies, cementing their place as pivotal machinery in the global manufacturing ecosystem.