1. Equipment Composition
-
-
-
Decoiler (hydraulic/pneumatic)
-
End Shear & Butt Welder
-
Accumulator/Looper
-
Forming Mill Section
-
High-Frequency Welding Unit
-
Inner and Outer Weld Bead Removal
-
Water Cooling System
-
Sizing and Straightening Section
-
Automatic Flying Cut-Off System
-
Discharge Conveyor and Table
-
Electric Control System (PLC-based)
2. Technical Parameters
-
Wide Specification Range: Suitable for producing multiple pipe diameters and thicknesses.
-
High Weld Quality: Efficient induction welding delivers strong and narrow weld seams.
-
High Automation: Real-time adjustment and diagnostics ensure stable operation.
-
Modular Design: Simplifies maintenance and future upgrades.
-
Energy Efficient: Optimized power control lowers energy consumption.
4. Welding Process Overview
-
Utilizes solid-state high-frequency welders, typically 200–500KHz.
-
Magnetic rods or impedance devices help concentrate heat at the weld edges.
-
Optional automatic lifting inner weld bead scraper ensures internal cleanliness.
-
Weld seam is rapidly cooled and straightened post-welding.
The Technical Flow of the Production Line
Steel coil → Uncoiling → Shear & End Welding → Accumulating → Forming → HF Welding → Inner burr removal → Outer burr removal → Cooling → Sizing → Straightening → Cutting → Run-out → Packaging
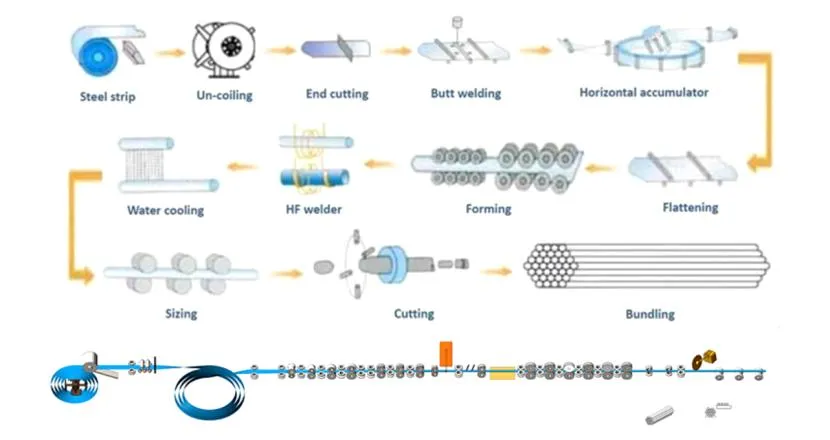
5. Packaging and Transportation:
-
Machine modules are film-wrapped and fixed in steel frames.
-
Electrical and hydraulic parts are packed in moisture-proof wooden boxes.
-
Each shipment includes a user manual, wiring diagram, and spare parts list.
-
Export standard compliant with CE, ISO, and customer destination customs requirements.