The Induction Coil is a key component in welded pipe production lines, commonly used in high-frequency welding processes. It works by generating high-frequency currents through electromagnetic induction, which locally heats the pipe surface to the required welding temperature, thus enabling efficient and high-quality welding. The induction coil is typically used in conjunction with a high-frequency power supply to ensure stable and efficient welding. It plays a vital role in the welding of various materials, such as steel pipes, seamless pipes, and galvanized pipes, in welded pipe production.
2. Working Principle
The working principle of the induction coil is based on electromagnetic induction heating. When an electric current passes through the coil, it creates a changing magnetic field around it. According to Faraday's law of electromagnetic induction, this magnetic field induces high-frequency currents in the pipe, which generates heat (Joule heat) on the surface and interior of the pipe, raising the pipe to the desired welding temperature.
The specific process is as follows:
-
Current flows through the coil: The high-frequency power supply sends high-frequency current to the induction coil.
-
Magnetic field generation: The alternating current passing through the coil generates a changing magnetic field that passes through the pipe and induces currents in the pipe's surface.
-
Pipe heating: The induced currents in the pipe generate Joule heat, which heats the pipe to the required welding temperature (typically between 800°C and 1200°C).
-
Welding: The heated pipe edges soften and are fused together under pressure to form a strong welded joint.
The induction coil allows for control over the heating zone and depth by adjusting the frequency and current intensity, ensuring the precision and consistency of the welding process.
3. Technical Specifications
This table provides the typical technical specifications for induction coils used in welded pipe equipment. Specific parameters can be adjusted and customized based on the production line's requirements.
4. Main Components
-
Coil Body:
-
The coil is the core component of the induction heating system, typically made from copper tubing for high electrical conductivity. The coil shape (e.g., circular, spiral) is closely related to the pipe specifications and welding requirements.
-
High-Frequency Power Supply:
-
Cooling System:
-
Since the induction coil generates significant heat during operation, a cooling system is crucial. Typically, a water-cooling system circulates coolant through pipes to remove the heat and maintain the coil at a safe operating temperature.
-
Oscillator and Adjustment Device:
-
Insulation Layer:
-
Sensors and Control System:
5. Summary
The induction coil plays a key role in welded pipe equipment by providing stable and precise heating to the pipe through electromagnetic induction, ensuring efficient and high-quality welding. Its main features include the flexibility of the high-frequency power supply, high electrical conductivity of the coil, and a comprehensive cooling and control system. With proper configuration and optimization, the induction coil significantly improves welding quality, reduces energy consumption, and increases production efficiency. Therefore, it is an essential component in modern welded pipe production lines.
-
-
- 1. Coil car and Storage
- 2.Single And Double Heads Un-coiler & Hydraulic And Pneumatic Un-coiler
- 3.Peeler and hold down roll arm
- 4.Flattening Machine
- 5.Automatic and Semi Auto Shearer & Butt Welder
- 6.Vertical Cage Accumulator & Horizontal Loop Accumulator & Landing Horizontal Spiral Loop Accumulator
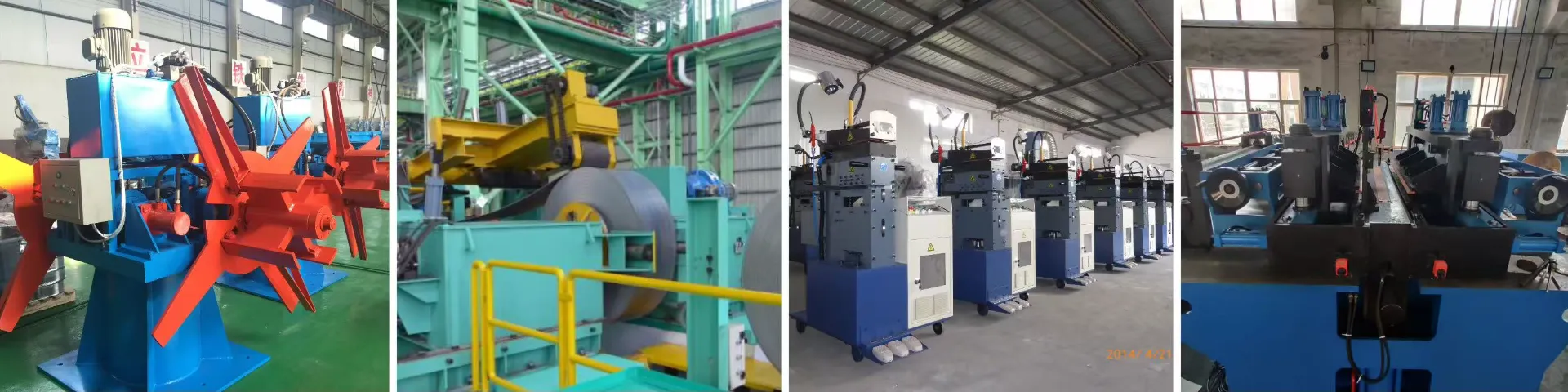
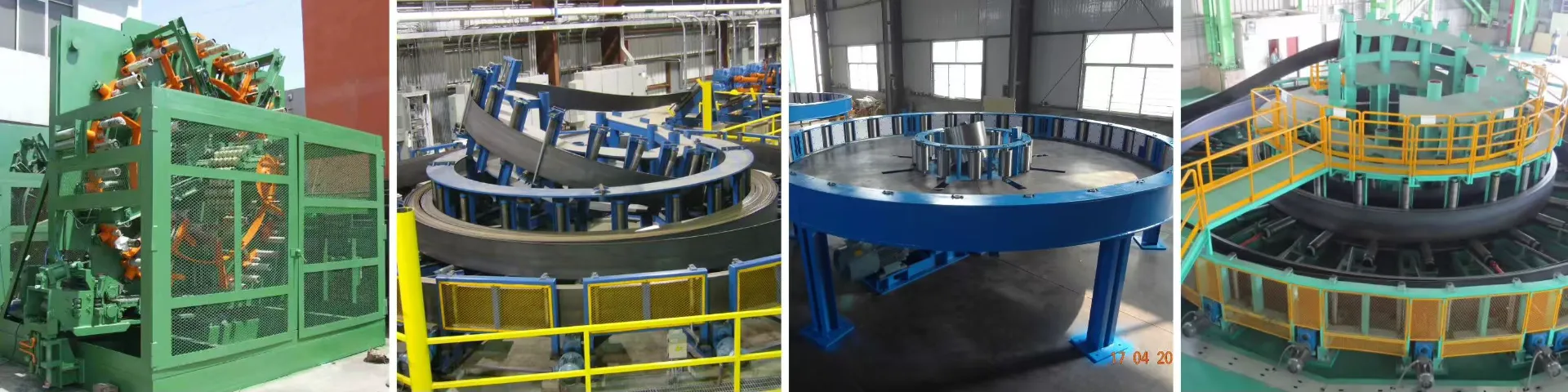
-
- 1. 渦電流検査装置
- 2. シームアニーリングマシン
- 3. ストレートアイロン
- 4. 面取り・端面加工機
- 5. ハイドロテスター
- 6. ねじ切り機
- 7. 塗装・オイルマシン
- 8. 自動バンドル包装機
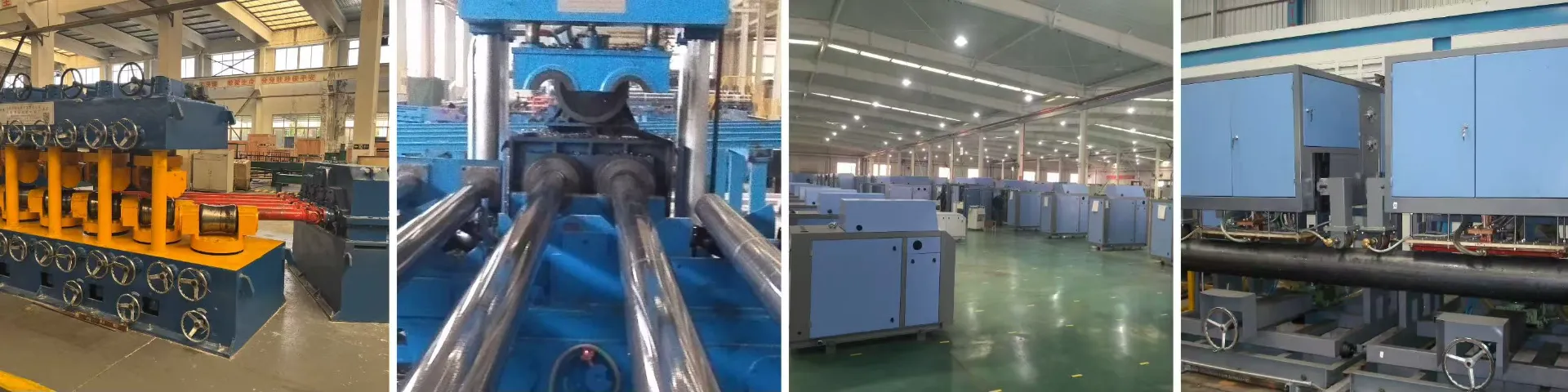
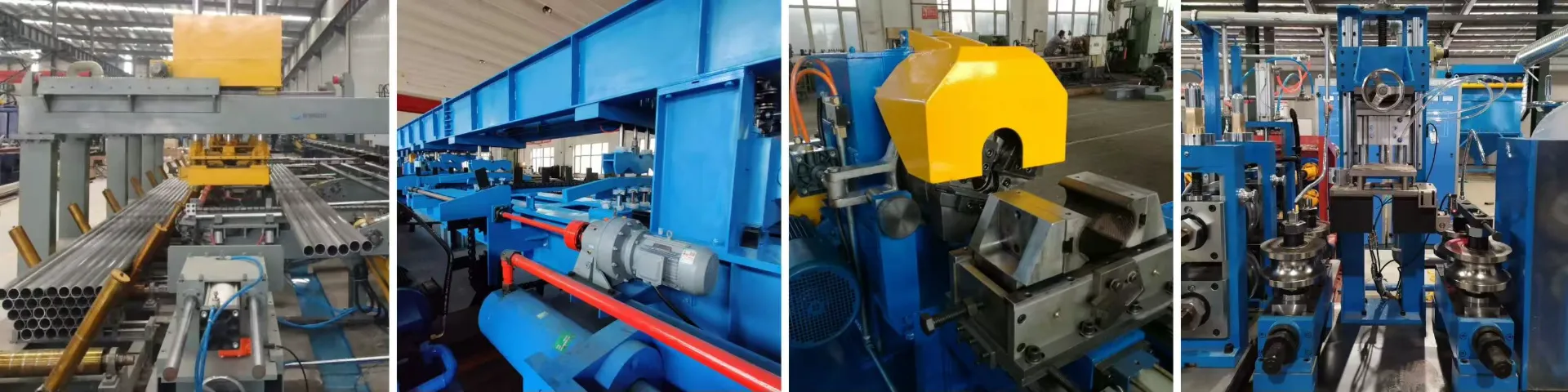
Spare Parts and Consumble Parts
-
- 1. Rollers, Moulds, Dies, D2,D3 material to choose
- 2. フェライト、インピーダー、グラスファイバーチューブ
- 3. HSS鋸刃、TCT鋸刃、摩擦鋸刃
- 4. ODバリ取りインサート、IDバリ取りインサート
- 5. HF溶接機誘導コイルおよびその他のHF溶接機スペアパーツ
- 6. 誘導コイル用銅管、誘導コイル用PTFEパイプ
- 7. MOSFET、ボード
- 8. 鋼管結束機
- 9. 亜鉛スプレーマシン、亜鉛ワイヤー、亜鉛スプレーガン
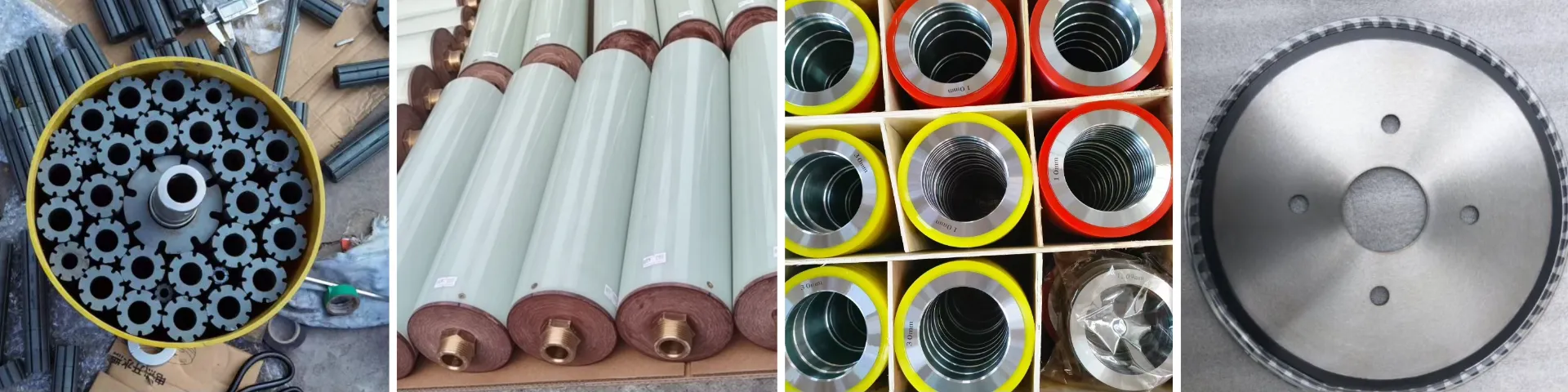
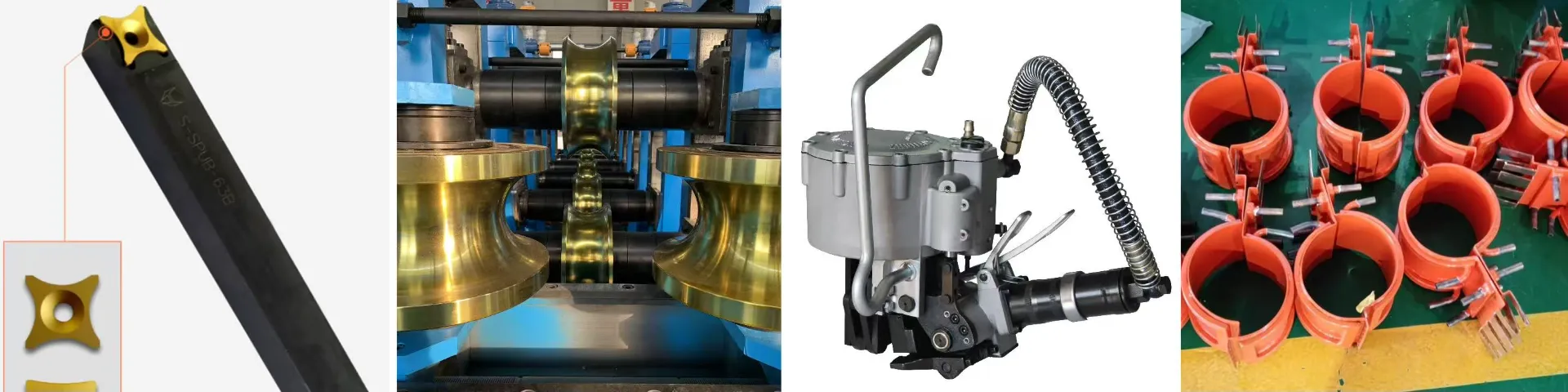
- 当社を選ぶ理由
-
1.Leading Technology, Reliable Quality, Excellent Service! 最適化されたデザイン、高品質の素材を選択! 熱処理工程保証!
-
2.Spiral bevel gear, drum gear coupling and carburization. ギア歯の焼入れ。 駆動システムは安定性、効率性、装着性、低ノイズを実現。
-
3.High precision wear resisting and Long life of toolings. すべての機械旋盤、キー溝は CNC によって位置決めおよびフライス加工されます。
-
4.Quality department make sure the material of the raw materials quality, and ensure the machine running perfect.
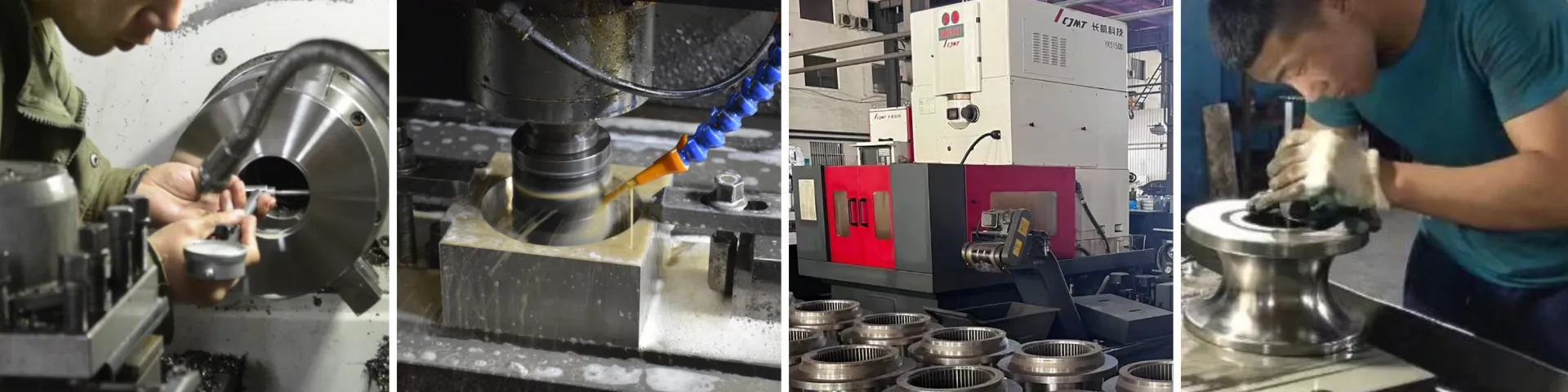
アフターサービス
- 1.Machine test running videos will supply to customer before shipment.
- 2.Online techenical support WHOLE LIFT FREE.
- 3.Professional engineers team to install the machine, train your employee well.
- 4.One year warranty and life-long technical support.
- エンジニアの対応には5~24時間かかります。
- 6. お客様と当社とのビジネス関係はいかなる第三者に対しても秘密にされます。
- 7. We welcome customers to visit our factory anytime.
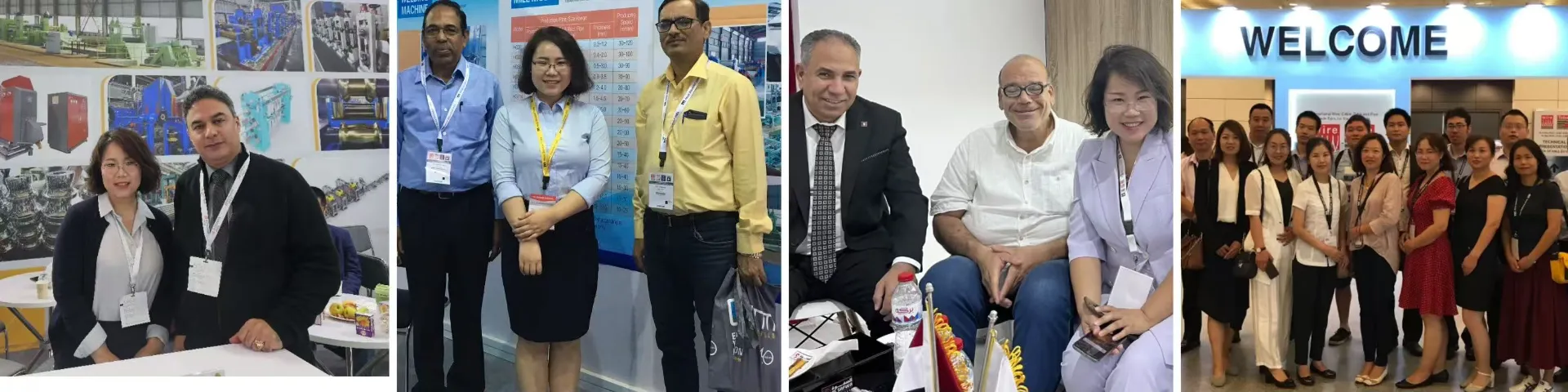