Solid-state welding represents a transformative chapter in the realm of welding technologies, garnering attention for its profound impact in industries that value precision and structural integrity. This article unfolds the varied types of solid-state welding techniques, focusing on their applications, advantages, and the nuances that set them apart.
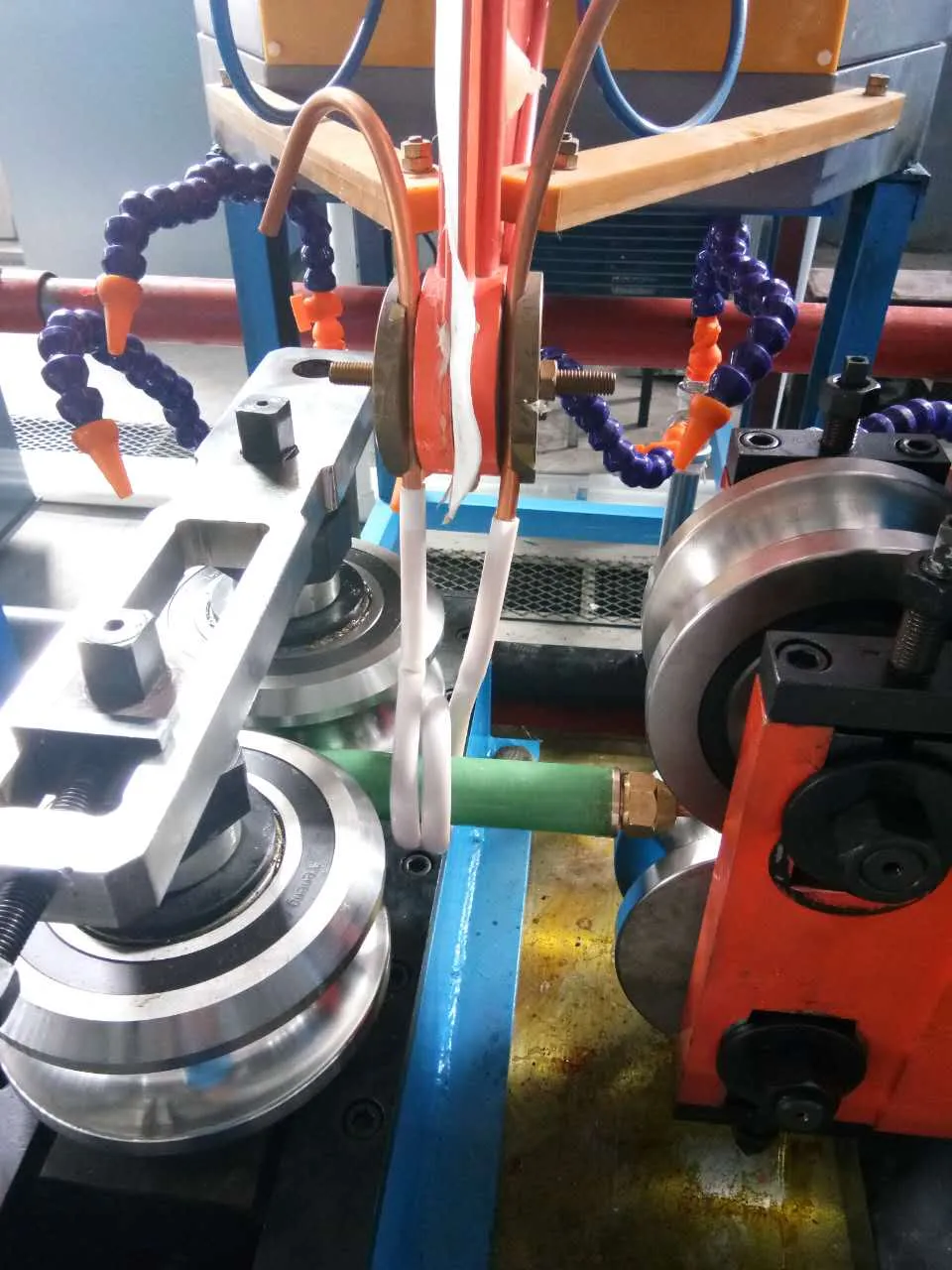
The cornerstone of solid-state welding is the creation of a welded joint without melting the base material. This is accomplished through the application of pressure, sometimes in combination with temperature, which results in a bond at the atomic level. The absence of melting means fewer defects typical of fusion welding processes, such as porosity and shrinkage, making solid-state welding ideal for critical applications.
Friction welding is perhaps the most iconic type within this family. This technique involves the generation of heat through mechanical friction between workpieces, followed by the application of axial pressure to forge the materials together. Variants such as friction stir welding (FSW) and rotary friction welding have carved niches in different sectors. FSW, for example, is acclaimed in the aerospace and automotive industries for its ability to join lightweight aluminum alloys with precision. It enhances mechanical properties and eliminates the risk of solidification cracks, a notable issue in conventional welding.
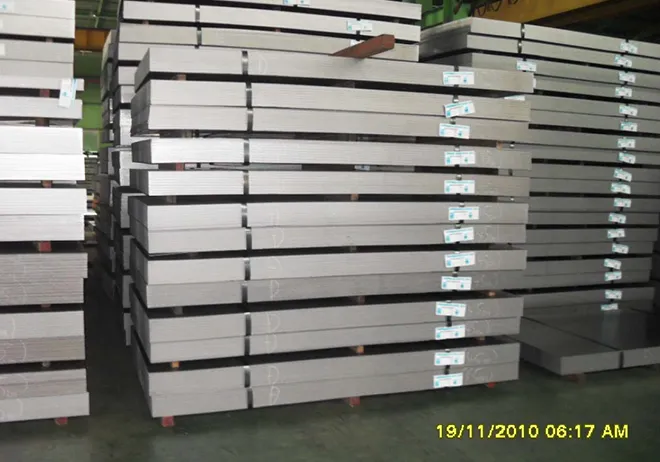
Diffusion bonding, on the other hand, is a process defined by the application of heat and pressure over an extended period, allowing atoms to migrate across the interface. This method is especially valuable in the aerospace industry and is trusted for manufacturing complex components like turbine blades and honeycomb structures. The exacting nature of diffusion bonding, requiring meticulously clean surfaces and controlled environments, underscores its stature among high-performance industries.
Another critical process is ultrasonic welding, which utilizes high-frequency ultrasonic vibrations to create solid-state welds. Widely used in the electronics and medical devices sectors, this method offers precision with minimal thermal impact on sensitive components. It's particularly advantageous for joining thin or delicate materials, including plastics and non-ferrous metals.
solid state welding types
Explosive welding, despite its dramatic name, is a highly controlled process where the force of an explosive charge is used to join two metal sheets. This technique is indispensable for creating clad metals and is praised in the petrochemical and marine industries for bonding materials that are normally un-weldable, such as titanium to steel.
Each of these methods brings a unique set of strengths. For instance, cold welding, which occurs without any heat, is significant in environments where heat could compromise material properties. This process has been revolutionary in the electronics industry, where it enables the layer-by-layer fabrication of micro-components.
The decision to use a particular solid-state welding technique is dictated by various factors, including material compatibility, joint configuration, and the specific performance criteria of the final product. For entities aiming to optimize their manufacturing processes, understanding the subtleties of each process is critical. By choosing the right method, companies can ensure superior joint quality, component longevity, and overall performance.
To harness the full potential of solid-state welding, it's imperative to stay informed on advancements through continuous research and development. As industries push boundaries, adopting these welding technologies not only fulfills current needs but also strategically positions an organization ahead in a competitive market. Through vigilant quality control and robust testing, the trust in these methodologies is further reinforced, delivering reliable and lasting solutions tailored to the demands of modern engineering.