🔧 1. Slitting Knives
Slitting knives are the core cutting components used in slitting lines. They are designed to longitudinally slit wide steel coils into narrower strips. Suitable for a wide range of materials including stainless steel, carbon steel, galvanized steel, silicon steel, and aluminum.
Features:
-
Premium Materials: Commonly used materials include alloy tool steel and powder metallurgy high-speed steel (e.g., D2, SKD11, H13, Cr12MoV, ASP2053).
-
High Hardness: HRC 58–65 for excellent wear resistance and long service life.
-
Sharp Edges: Ensure clean cuts with minimal burrs.
-
Precise Heat Treatment: Delivers superior heat resistance and fracture toughness.
🧩 2. Slitting Spacers
Slitting spacers are placed between slitting knives to maintain consistent knife spacing and ensure precise slitting. They are essential for knife gap adjustment, positioning, and cushioning.
Features:
-
High Dimensional Accuracy: Tolerance up to ±0.001 mm.
-
Durable Materials: Typically made from high-hardness tool steel or stainless steel.
-
Surface Finishing: Includes black oxide, chrome plating, or nickel plating.
-
Various Types Available: Includes rubber spacers, metal shims, and solid precision spacers.
-
-
📊 Technical Specifications (Sample Table)
Item |
Slitting Knife |
Slitting Spacer |
Material |
D2 / Cr12MoV / SKD11 / H13 |
65Mn / Cr12 / Stainless Steel |
Hardness (HRC) |
58–65 |
50–60 |
Outer Diameter (mm) |
Ø80 – Ø500 |
Ø80 – Ø500 |
Bore Tolerance |
H7 (customizable) |
H7 (customizable) |
Thickness Range |
0.8 – 30 mm (customizable) |
0.5 – 20 mm (customizable) |
Flatness |
≤0.002 mm |
≤0.0015 mm |
Concentricity |
≤0.01 mm |
≤0.005 mm |
Surface Finish |
Polished, Nitrided, Chrome-plated, etc. |
Nickel-plated, Blackened, Anti-rust oil |
🛠 Maintenance Guidelines
🔪 Slitting Knives
-
Regular Sharpness Check: Regrind when burrs appear or cutting quality declines.
-
Use Proper Cleaning Agents: Avoid metal debris buildup on the blade edge.
-
Storage: Keep knives separated using dedicated racks or boxes to avoid chipping.
-
Regrinding Schedule: Typically every 8–12 hours of cutting, depending on material hardness.
-
Avoid Overheating: Control cutting pressure and speed to prevent annealing or deformation.
🧩 Slitting Spacers
-
Avoid Scratches and Damage: Ensure spacer surfaces remain smooth for precise positioning.
-
Rust Prevention: Apply anti-rust oil regularly and clean before use.
-
Dimensional Calibration: Verify thickness when adjusting for different material gauges.
-
Labeled Storage: Store different thicknesses separately and clearly marked to prevent mix-up.
-
📊The comparison table for rubber-coated spacers, rubber rings, and washers used in steel coil slitting lines:
Item |
Rubber-Coated Spacer |
Rubber Ring |
Washer / Shim |
Purpose |
Installed between slitting knives to control slitting width and spacing, and to prevent coil surface damage |
Typically used for shock absorption, cushioning, or sealing gaps between tools/shafts |
Used for precise adjustment of slitting gaps or compensating dimensional deviations |
Structure |
Metal spacer core coated with a rubber layer |
Entirely made of rubber in ring shape |
Made of metal, rubber, or composite material with high thickness precision |
Material |
Composite of metal and rubber |
Rubber |
Commonly metal, but can also be rubber or plastic |
Functional Features |
Prevents direct contact between tools, provides cushioning and protection |
Acts as a buffer, prevents loosening, and seals |
Ensures precise positioning and dimensional compensation |
Thickness Range |
Generally several millimeters to over ten millimeters |
Thinner, primarily for elastic cushioning |
High precision, thickness can be controlled to 0.01 mm or less |
Installation Location |
Mounted on the shaft between knives or spacers |
Installed at shaft or spacer interfaces |
Used where fine gap adjustment is required, e.g., between knives or shaft ends |
Application |
Suitable for protecting coil edges and preventing damage |
Suitable for sealing or vibration-damping |
Suitable for fine-tuning dimensions or ensuring precise fit |
-
-
- 1. Coil car and Storage
- 2.Single And Double Heads Un-coiler & Hydraulic And Pneumatic Un-coiler
- 3.Peeler and hold down roll arm
- 4.Flattening Machine
- 5.Automatic and Semi Auto Shearer & Butt Welder
- 6.Vertical Cage Accumulator & Horizontal Loop Accumulator & Landing Horizontal Spiral Loop Accumulator
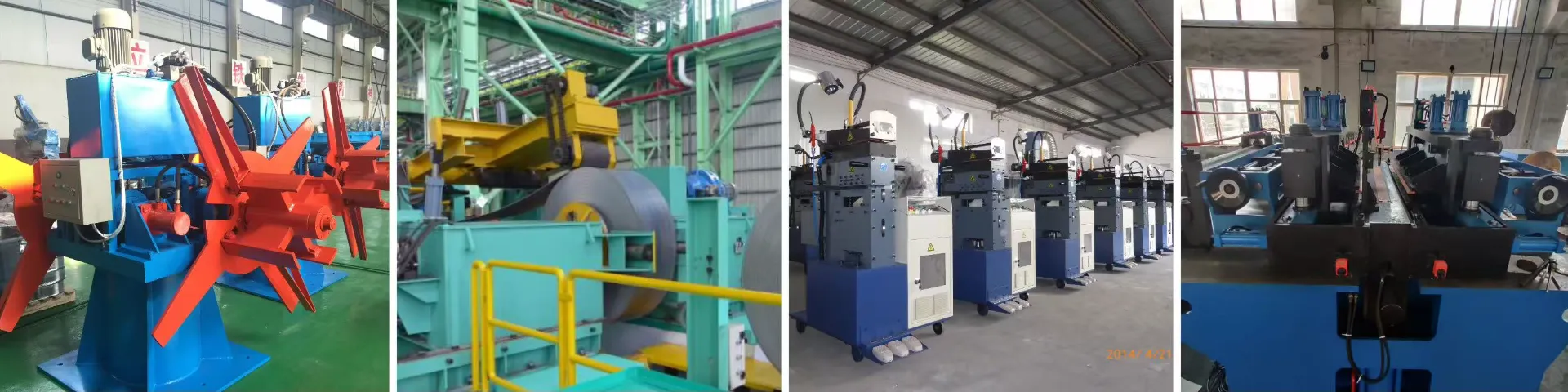
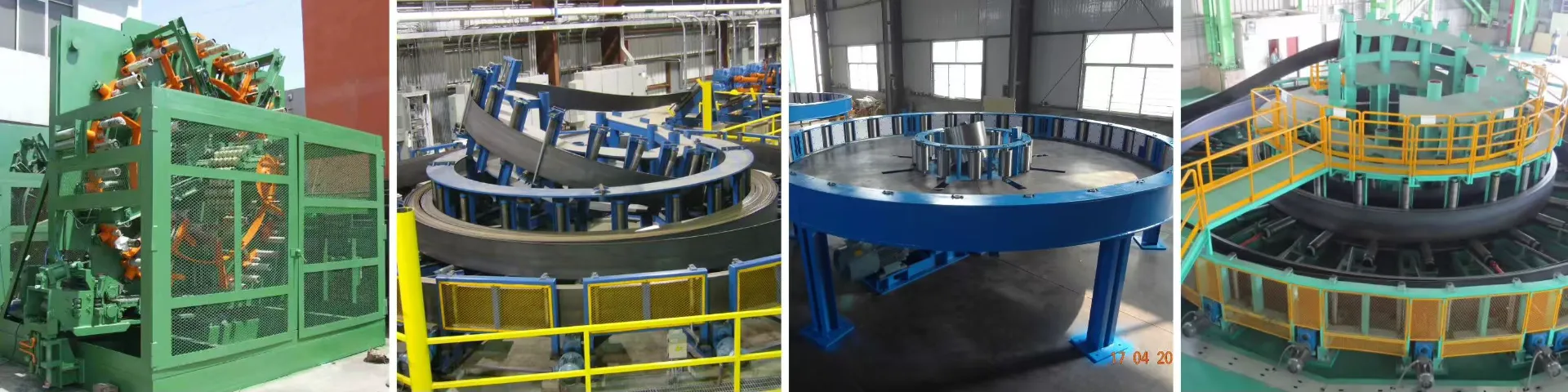
-
- 1. Eddy current machine
- 2. Seam annealing machine
- 3. Straightener machine
- 4. Chamfer and end facer machine
- 5. Hydro Tester machine
- 6. Threading machine
- 7. Painting and oil machine
- 8. Automatic bundle and package machine
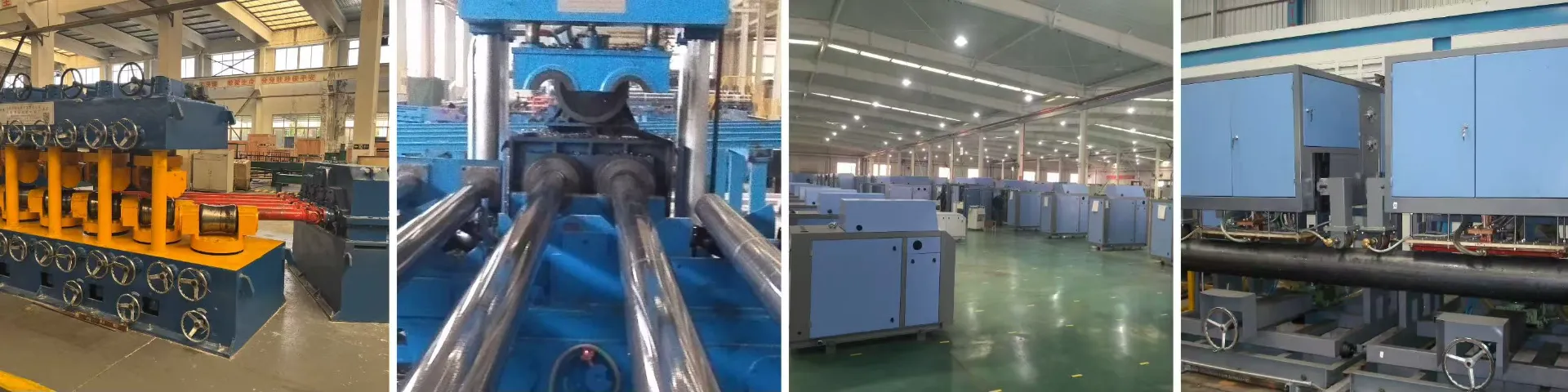
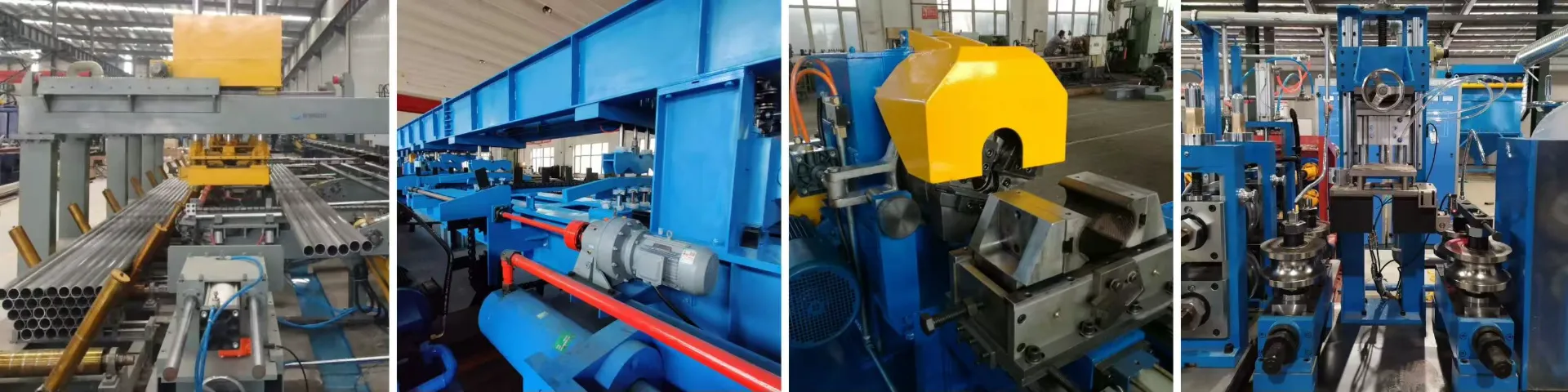
Spare Parts and Consumble Parts
-
- 1. Rollers, Moulds, Dies, D2,D3 material to choose
- 2. Ferrite, Impeder, Fiberglass tube
- 3. HSS saw blades, TCT Saw blades, Friction saw blades
- 4. OD burr remove inserts, ID burr remover inserts
- 5. HF welder Induction Coil and other HF welder spare parts
- 6. Copper tube for induction Coil, PTFE pipe for Induction Coil
- 7. Mosfet, Boards
- 8. Steel pipe Strapping machine
- 9. Zinc Spray Machine, Zinc wire, Zinc spray gun
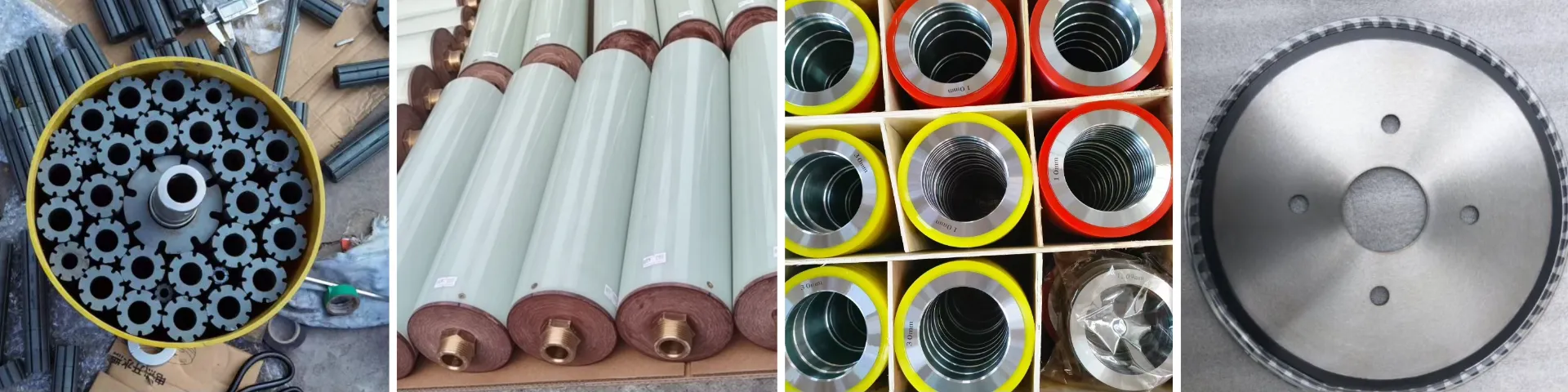
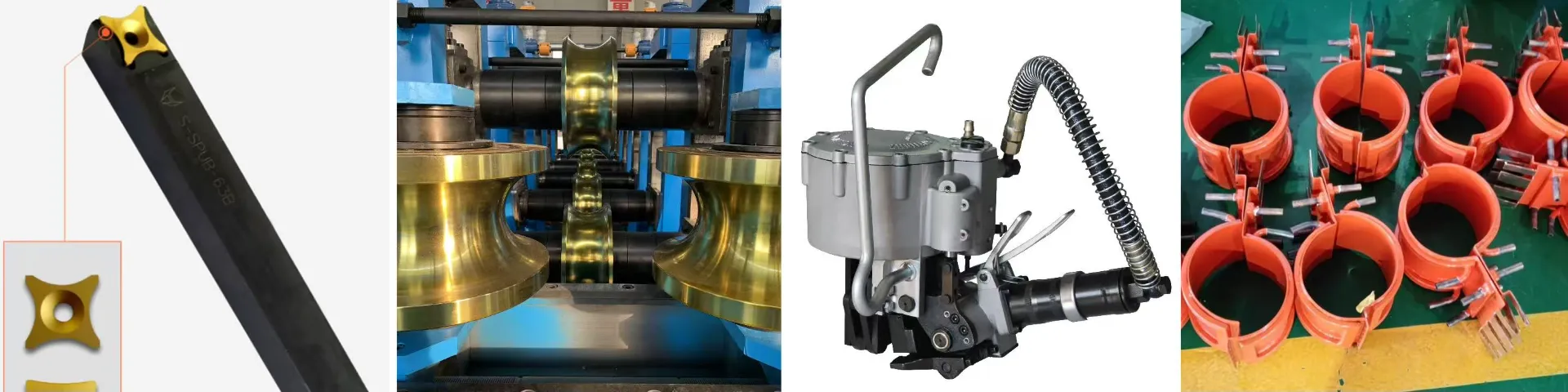
- Why Choose Us?
-
1.Leading Technology, Reliable Quality, Excellent Service! Optimized Design, High quality material select! Heat treatment process guarantee!
-
2.Spiral bevel gear, drum gear coupling and carburization. Gear teeth quenching. Driven system stable, efficient and wearable with lower noise.
-
3.High precision wear resisting and Long life of toolings. All the machine Lathes, Key Grooves are positioned and Milled by CNC.
-
4.Quality department make sure the material of the raw materials quality, and ensure the machine running perfect.
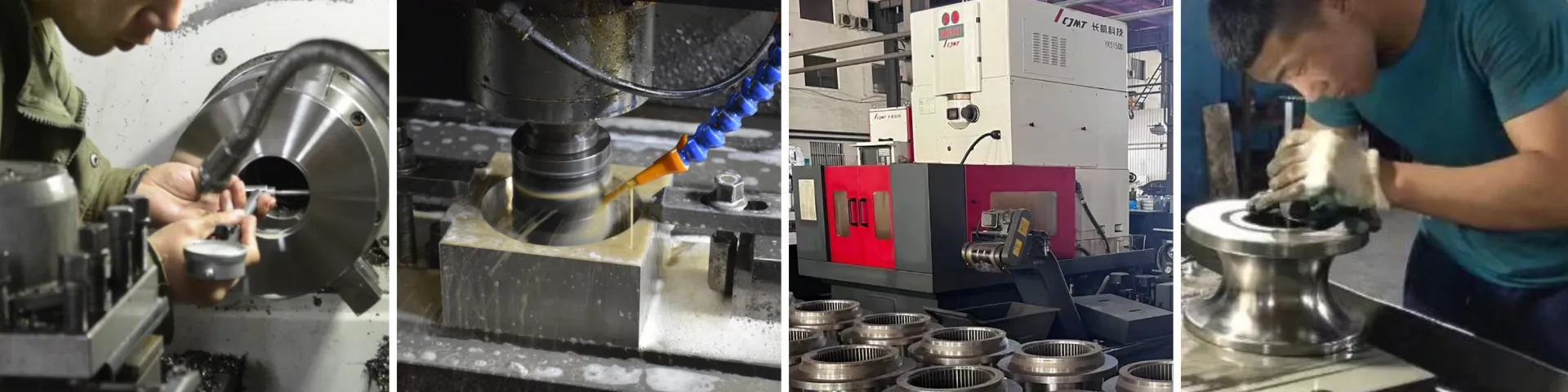
After-sales service
- 1.Machine test running videos will supply to customer before shipment.
- 2.Online techenical support WHOLE LIFT FREE.
- 3.Professional engineers team to install the machine, train your employee well.
- 4.One year warranty and life-long technical support.
- 5 .24 hours for engineer response.
- 6.Your business relationship with us will be confidential to any third party.
- 7. We welcome customers to visit our factory anytime.
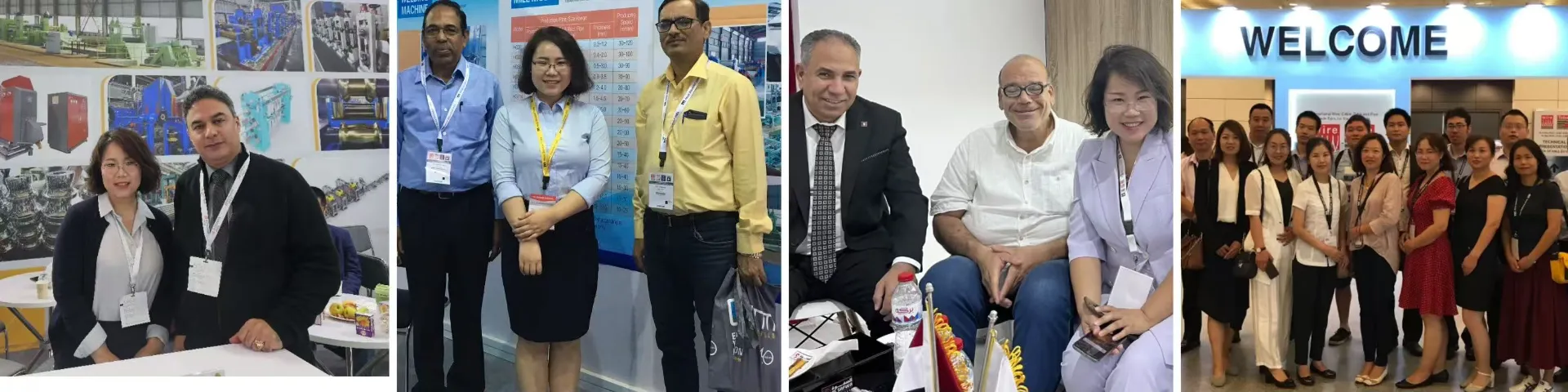