-
Wide Size Range: Capable of producing ERW pipes with diameters from Φ114mm to Φ325mm, covering most large-size industrial demands.
-
Strong Welding Capacity: Equipped with high-power HF induction welding machines, stable for thick-wall materials.
-
Flexible Roll Tooling System: Quick mold change design reduces downtime and supports various pipe sizes.
-
Fully Automated Control: Centralized PLC control with HMI touch screen, easy to operate and adjust.
-
Modular Design: Easy for installation, maintenance, future upgrades, and remote support.
List of Equipment Supply
Coil Loading → Uncoiling → Shear & Butt Welding → Accumulator → Forming → HF Welding → Deburring → Cooling → FFX Sizing/Forming → Flying Saw Cutting → Straightening → Hydrostatic Testing → Oiling/Painting → Automatic Bundling
No. |
Equipment Name |
Function Description |
1 |
Hydraulic Coil Car + Uncoiler |
Loads and uncoils steel coil with auto tensioning; supports heavy coils |
2 |
Shear & Butt Welder |
Connects two coils end-to-end without stopping the main line |
3 |
Accumulator |
Maintains strip supply during coil change |
4 |
FFX Forming Mill |
Flexible forming system that auto-adjusts roll positions for round and square tubes |
5 |
HF Induction Welding Machine |
Precisely welds the strip edges using high-frequency induction |
6 |
Inner & Outer Deburring Device |
Removes weld flash to improve pipe appearance and quality |
7 |
Water Cooling Spray System |
Rapid cooling of weld seam and full pipe to maintain shape |
8 |
FFX Sizing & Shaping Unit |
Finely adjusts outer diameter and shapes square/rectangular tubes |
9 |
Flying Saw Cutting System |
High-speed synchronized pipe cutting; hot saw, cold saw, or milling cutter available |
10 |
Quick Roll Change Unit |
Enables fast mold changes to minimize downtime and labor |
11 |
Straightening Machine |
Corrects pipe axis bending and improves straightness |
12 |
Hydrostatic Testing Machine |
Pressure testing for strength/sealing per API 5L/5CT standards |
13 |
Oiling/Painting Unit |
Applies anti-corrosion oil or paint to pipe surfaces |
14 |
Automatic Pipe Bundling System |
Automatically counts, aligns, and straps finished pipes for packaging |
15 |
Central Control System (PLC + HMI) |
Manages line operations, alarms, data, and supports remote service |
2. BASIC DESIGN DATA
Design of the proposed line is based on following specification:
Forming and Sizing section FFX Forming Technology
FFX (Flexible Forming Express) is an advanced forming system that uses universal rolls in the open section and adjusts roller positions (up/down, left/right) to accommodate various pipe sizes and wall thicknesses. Key advantages:
-
🔄 Quick Changeover: Only sizing rolls need to be replaced, switching in 10–20 minutes
-
💰 Tooling Cost Saving: 80%+ roll sets are reusable across sizes
-
🎯 High Dimensional Accuracy: Enhances weld seam alignment and consistent outer diameter
-
⚙️ Smart Integration: Compatible with auto roll change carts and parameter memory systems
Quick Roll Change System Advantages:
-
The system allows fast replacement of full roll stands:
-
Rails or hydraulic carts slide out entire roll units
-
Single-button locking and positioning
-
Less than 20 minutes per changeover
-
Supports mold ID management and digital recipe storage
Finishing Auxiliary Equipment Description
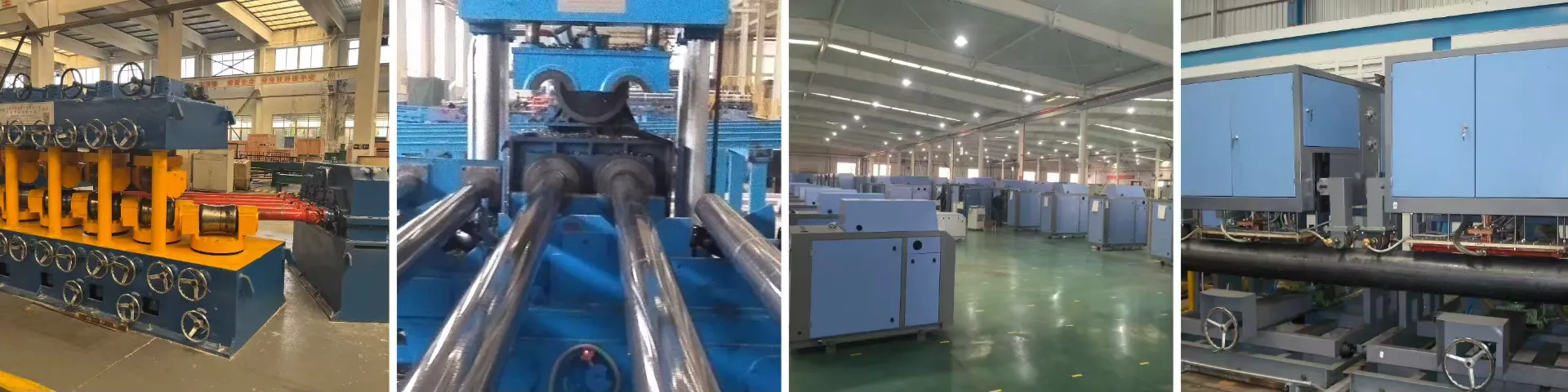
Operating Procedure
-
-
Product Applications
-