Inner Burr Removal Knife for ERW Tube Mills
During high-frequency welding of steel tubes, excess weld material often forms along the inner seam, creating internal burrs that can interfere with downstream processes or product quality. The inner burr removal knife is a critical tool designed to trim and smooth these internal weld protrusions in-line during tube production, especially for applications requiring high inner surface quality—such as in automotive tubing, furniture, and fluid transport systems.
Working Principle
The inner burr knife is typically installed after the welding section and before sizing. A precision-guided support mechanism feeds the knife head into the inner diameter of the tube, aligning it directly under the weld seam. As the tube continuously moves forward, the knife scrapes or shaves off the burr along the weld line. Some knife heads feature oscillating or rotary action to enhance trimming efficiency. Removed burr particles are discharged and collected via an external extraction system.
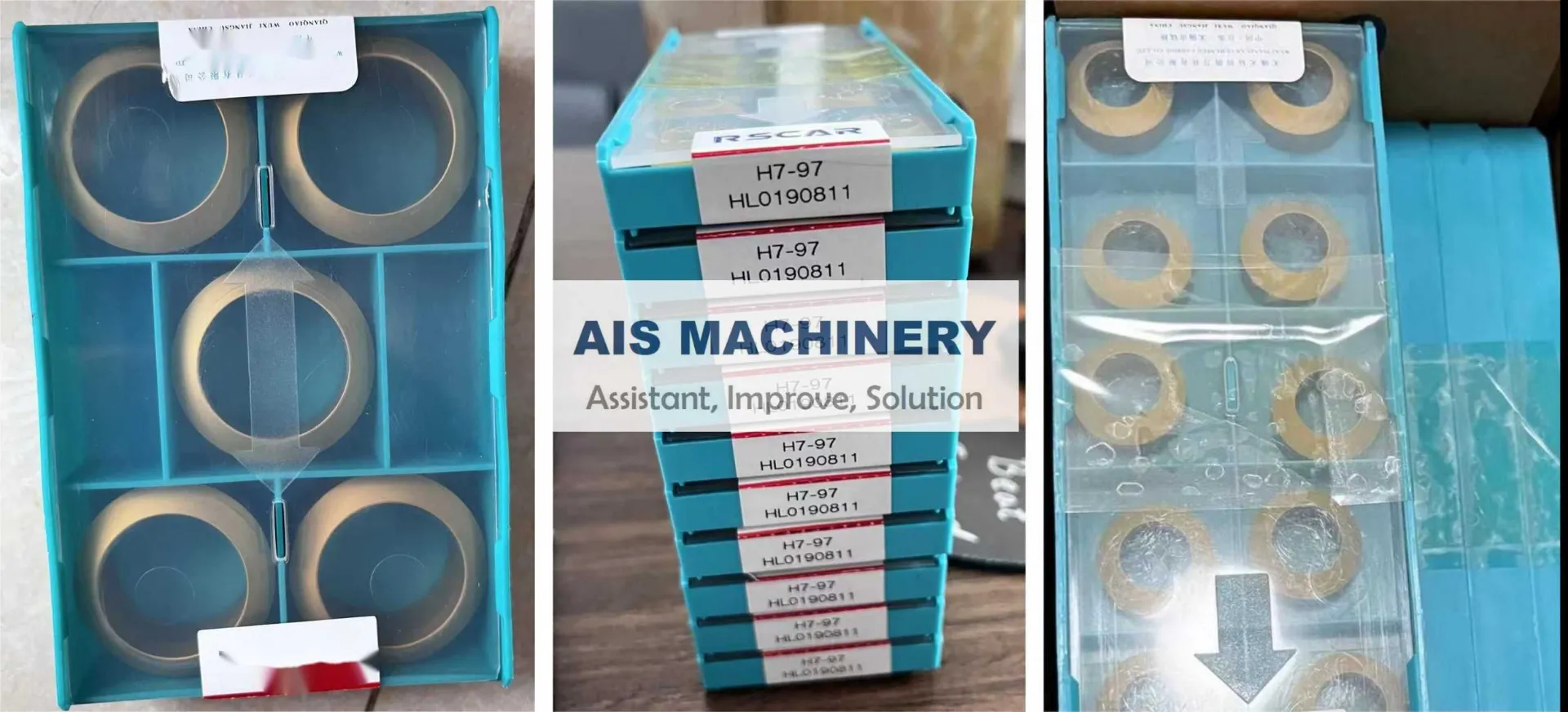
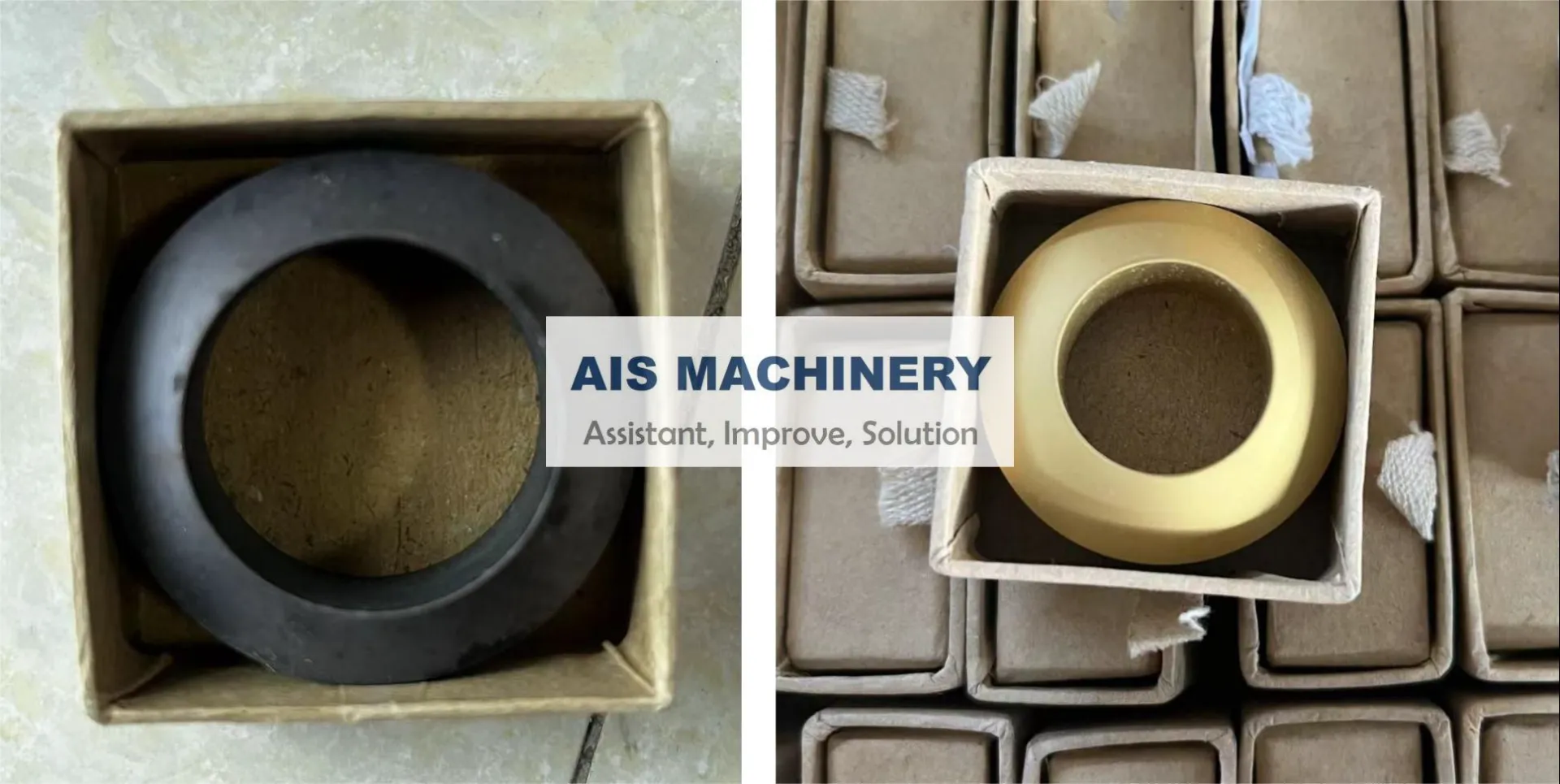
Key Specifications (customizable upon request)
-
Applicable Tube Diameter: Φ16 – Φ219 mm (larger sizes available)
-
Wall Thickness Range: 1.0 mm – 8.0 mm
-
Knife Material Options: Carbide steel, HSS (High-Speed Steel), Ceramic-coated
-
Offset Adjustment Range: ±3 mm (to align with weld seam position)
-
Knife Mounting System: Mechanical locking / Spring preload / Pneumatic-assisted
-
Cooling Options: Air-cooled / Water-cooled / Dry-cutting (depending on application)
Common Questions & Answers
Q1: Is burr removal always necessary?
Not always. For light-wall or general-purpose tubing, internal deburring may not be required. However, it's recommended for structural or high-spec applications.
Q2: How long does the knife last?
The knife is a consumable. HSS or carbide blades typically last 1–3 weeks depending on speed, material, and maintenance. Keep spare sets available for continuous operation.
Q3: Does the knife require precise weld alignment?
Yes. Poorly aligned or inconsistent welds can cause blade deflection or breakage. Weld quality should be stable before applying internal burr removal.
Q4: Is the knife easy to replace?
Yes. Most knife holders are designed for quick change, with replacement typically taking just a few minutes.
Usage Tips
-
Always align the knife precisely with the weld seam before operation.
-
For automated lines, use seam-tracking systems to optimize blade positioning.
-
If scratching or tube wall damage occurs, inspect blade sharpness and angle settings.
-
When changing tube diameters, use matching knife heads or inserts for best results.
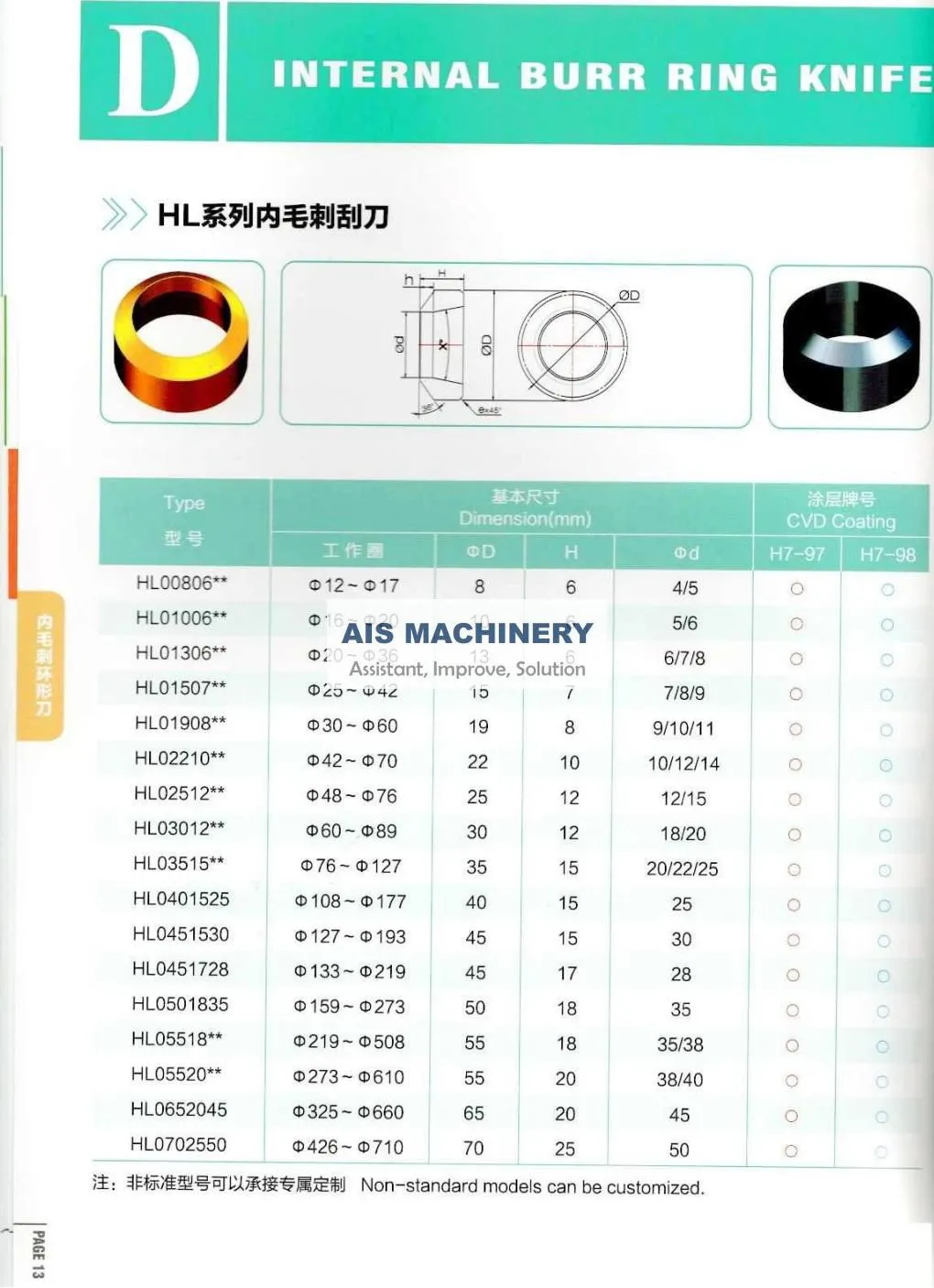
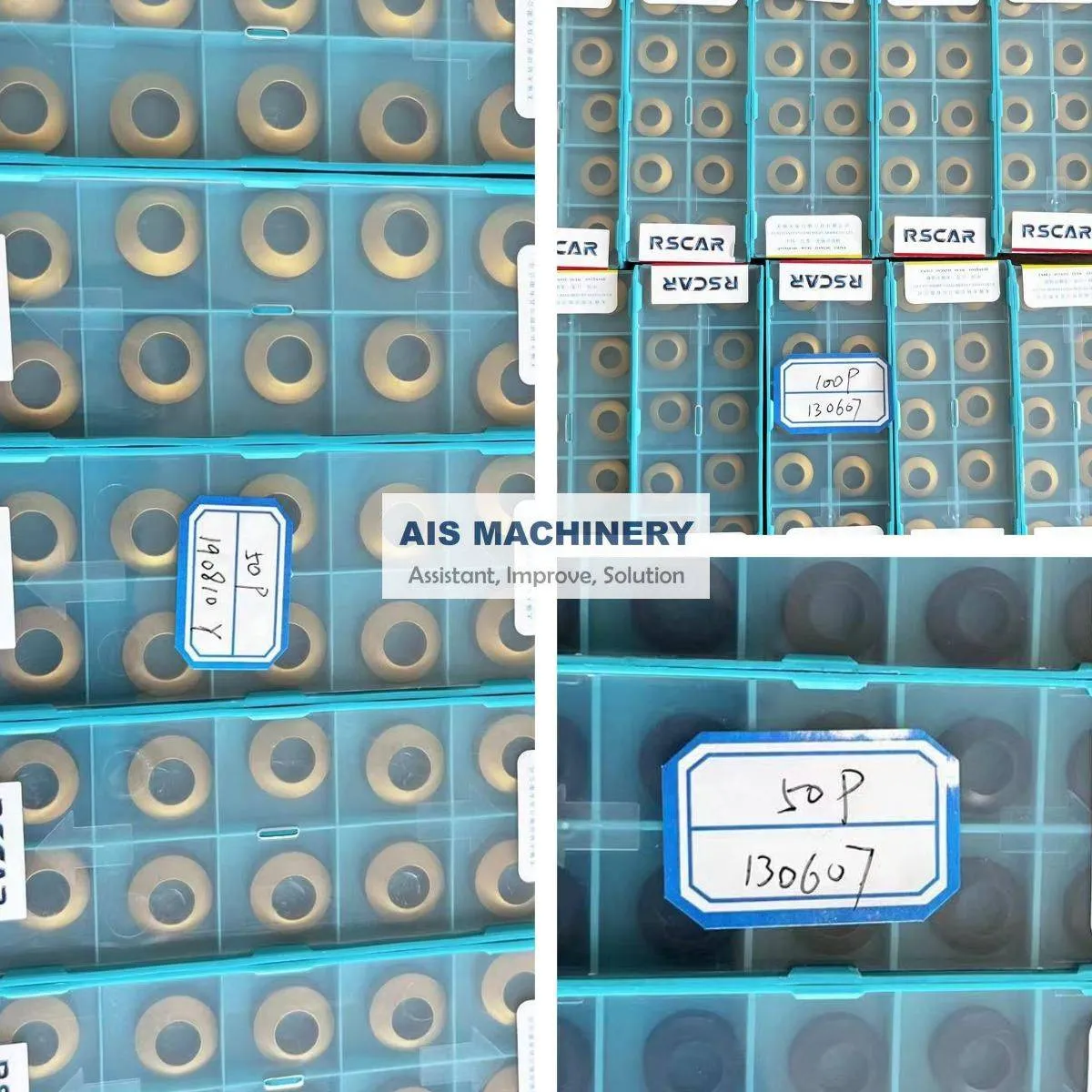
RELATION EQUIPMENT
We provides all equipment to tube mill entry section:
Coil Car
Single And Double Heads Un-coiler & Hydraulic And Pneumatic Un-coiler
Peeler and hold down roll arm
Flattening Machine
Automatic and Semi Auto Shearer & Butt Welder
Vertical Cage Accumulator & Horizontal Loop Accumulator & Landing Horizontal Spiral Loop Accumulator

TUBE MILL FINISHING SECTION
We provides all equipment to tube mill Finishing section:
1. Eddy current machine
2. Seam annealing machine
3. Straightener machine
4. Chamfer and end facer machine
5. Hydro Tester machine
6. Threading machine
7. Painting and oil machine
8. Automatic bundle and package machine

SPARE PARTS TO CHOOSE
Our Spare Parts Apply:
1. Roller, Mould, Cr12, Cr12Mov material, D2,D3 material
2. Ferrite, Impeder, Fiberglass tube
3. HSS saw blades, TCT Saw blades, Friction saw blades
4. OD burr remove inserts, ID burr remover inserts
5. HF welder Induction Coil and other HF welder spare parts
6. Copper tube for induction Coil, PTFE pipe for Induction Coil
7. Mosfet, Boards
8. Steel pipe Strapping machine
9. Zinc Spray Machine, Zinc wire, Zinc spray gun
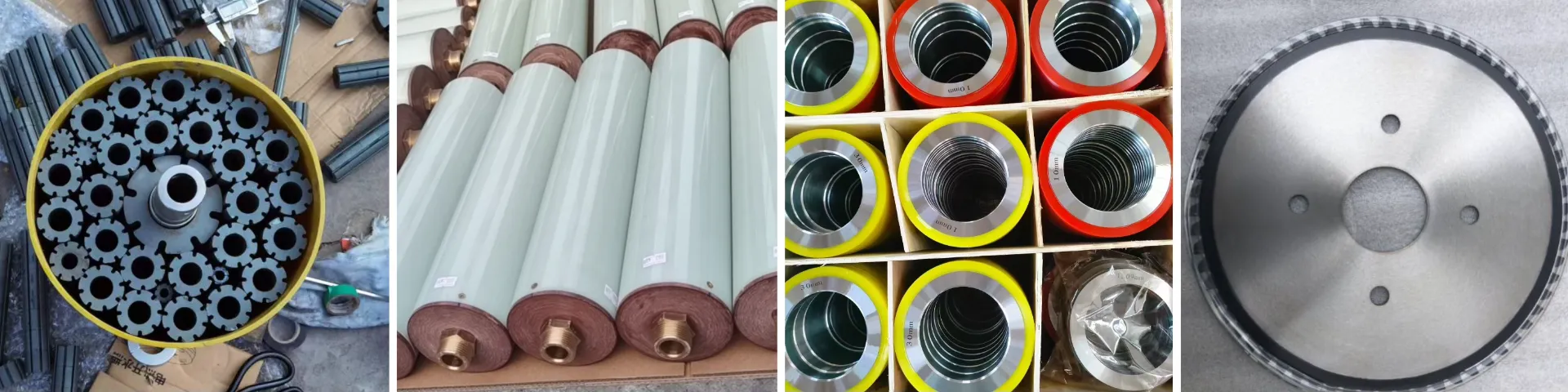
OUR CERTIFICATE

OUR SERVICE
Why Choose Us?
Leading Technology, Reliable Quality, Excellent Service!
Optimized Design, High quality material select!
Heat treatment process guarantee!
Spiral bevel gear, drum gear coupling and carburization.
Gear teeth quenching.
Driven system stable, efficient and wearable with lower noise.
High precision wear resisting and Long life of rollers.
All the machine Lathes, Key Grooves are positioned and Milled by CNC.
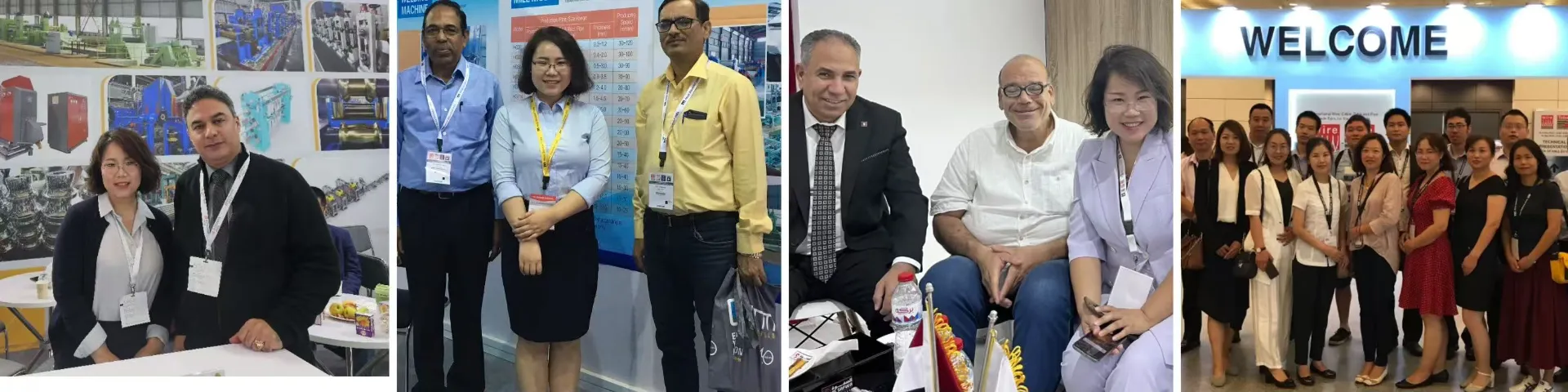
Our Service
Pre-sale service
1. We can provide machine running videos for reference
2. We will recommend the most suitable equipment according to the needs of customers
3. We can provide the layout of the factory
4. We welcome customers to visit our factory
After-sales service
1.We will delivery the machine and provide the documents on time to make sure you can get the machine quickly
2.When you finish the Preparation conditions, Our fast and professional aftersales service engineer team will go to your factory to install the machine, give you the operating manual, And train your employee until they can operate the machine well.
3.We provide one year warranty and life-long technical support.
4.Well-trained & experienced staff are to answer all your inquiries in English and Chinese
5 .24 hours for engineer response.
6.Your business relationship with us will be confidential to any third party.
Quality Control
We have the single quality department, that make sure the material of the raw materials is good, and ensure the machine running smoothly.
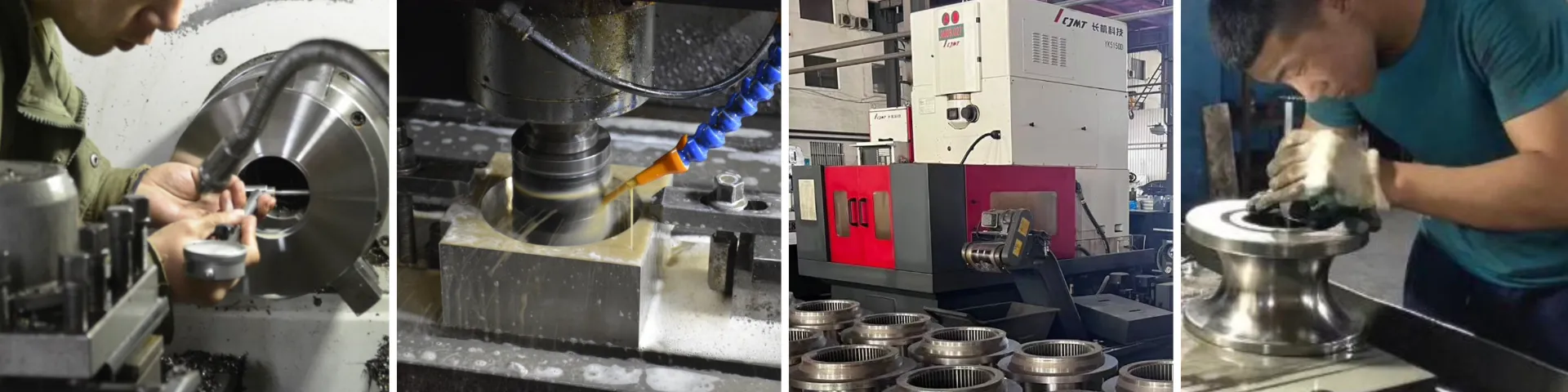