The production of cored wire tubes is a high-precision, high-efficiency cold roll forming process. The core challenge lies in ensuring uniform filling, consistent sealing, and continuous stable operation. The entire process integrates automated machinery with advanced control systems to meet the strict requirements of metallurgical refining.
1. Production Process
-
-
Steel Strip Decoiling
Premium cold-rolled low-carbon steel strips (typically 0.3–0.6 mm thick) are uncoiled and fed into the forming system.
-
Steel Strip Cleaning (Optional)
Surface cleaning or degreasing may be applied to enhance bonding and weld quality.
-
Pre-forming Stage
The strip is gradually bent into a "U" shape by rollers to prepare for core filling and sealing.
-
Precise Core Filling
Pre-blended metallic powders such as Ca, Al, Ti, Si, CaCO₃, or rare earths are dispensed into the U-shaped strip via a precision dosing system.
-
Tube Forming and Sealing
The filled strip is progressively formed into a closed tube. Sealing can be achieved through mechanical crimping or welding, ensuring no leakage.
-
Straightening and Compacting
Tubes are straightened and compacted to ensure dimensional consistency and core density.
-
Cut-to-Length
Tubes are cut into fixed lengths (e.g., 3m, 5m) or left continuous for coiling. Cutting tolerance is controlled within ±1%.
-
Coiling (if applicable)
Tubes are coiled into reels for efficient handling, transportation, and on-site feeding.
-
Quality Inspection and Packaging
Each batch undergoes visual inspection, weight verification, chemical sampling, and fill uniformity checks before final packaging.
2. Technical Parameters
-
Tube Specifications: |
Φ9mm, Φ13mm, Φ16mm, Φ20mm (customizable)
|
Wall Thickness: |
0.3 mm – 0.6 mm
|
Filling Ratio: |
10%–35% depending on application
|
Production Speed: |
30–80 m/min (up to 100 m/min under stable operation)
|
Poids de la bobine: |
150–500 kg per spool
|
Length Tolerance: |
±1%
|
-
-
- 3. Performance Standards After Use
-
-
Ultra-low sulfur structural steels
-
High-strength alloy steels
-
Pipeline steel, spring steel
-
Marine steel, automotive steel, premium-grade welded pipe steel
Additional Notes
-
Full production line equipped with a PLC-based control system for real-time monitoring and feedback
-
Optional in-line weighing systems to ensure consistent core material dosing
-
Custom solutions available including weld inspection units and laser measurement modules
-
The Technical Flow of the Production Line
{Steel Tape}→→ Double-head un-coiler →→Strip-head Cutter and welder→→Spiral accumulator→→Forming section(Flattening unit +Main driving unit +Forming unit +Guide unit +squeeze roller)+ De-burr frame →→Cooling unit →→ Sizing unit and straightener →→Recoiler
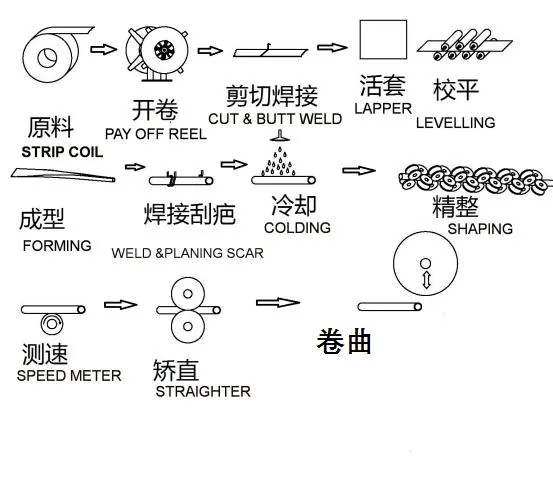